Custom Hydraulic Stamping Press
Youtube Video
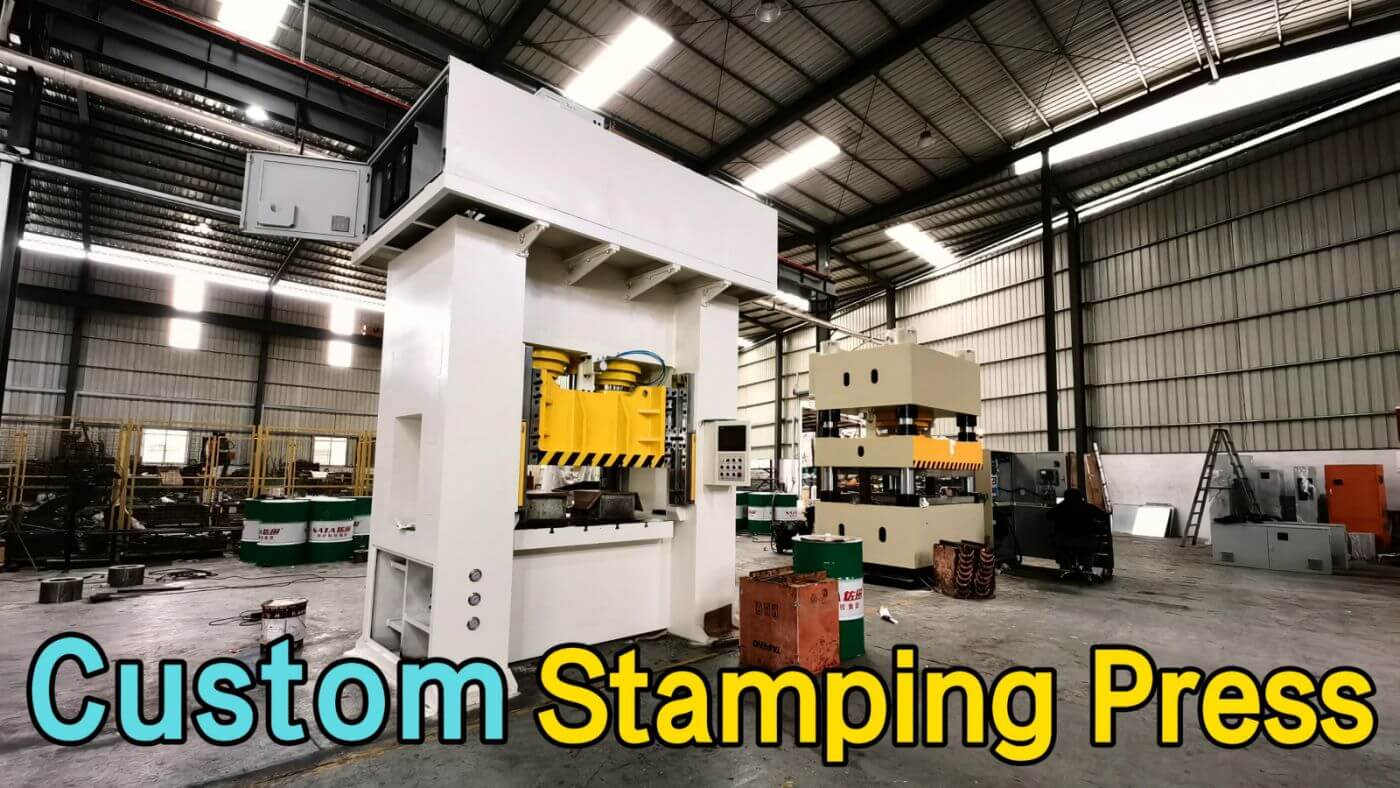
Hydraulic Stamping Press Components
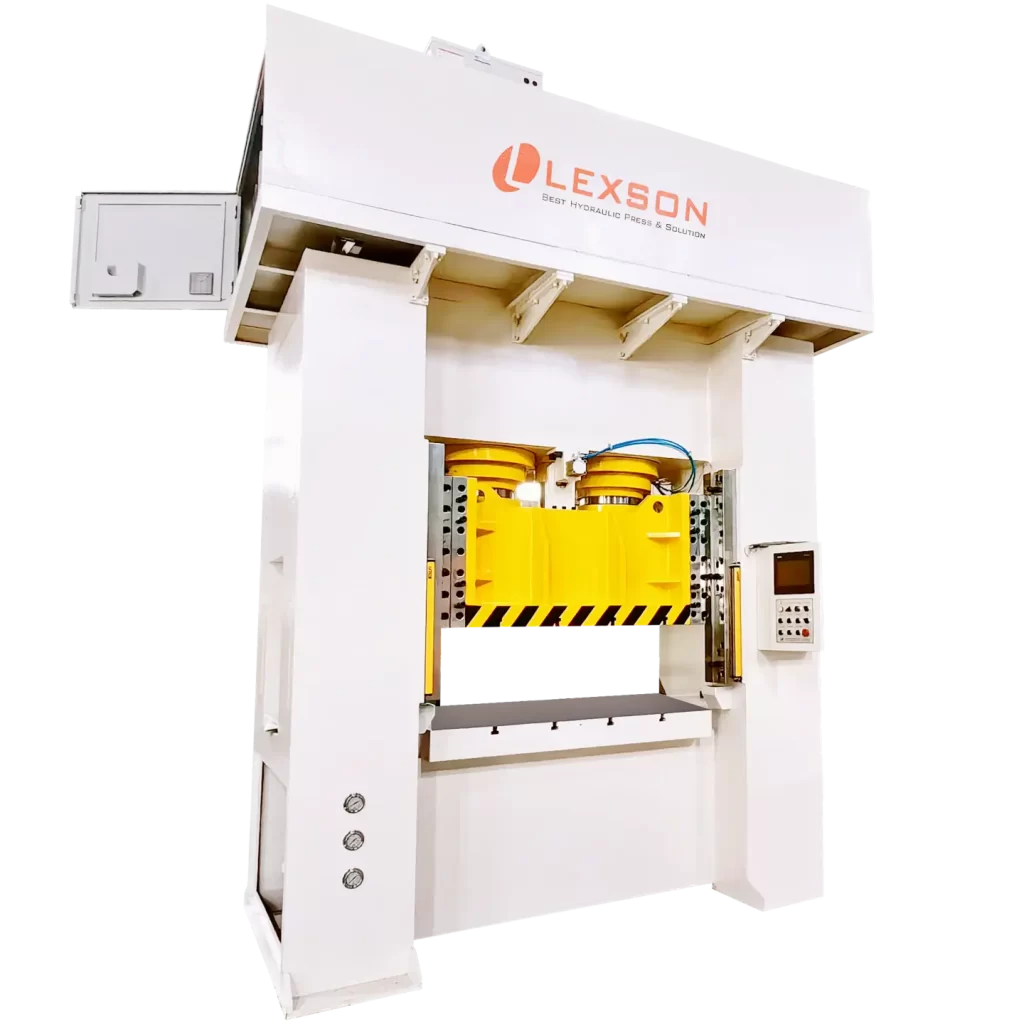
Electrical Box:
The main components of the electrical box come from Schneider (France) and Siemens (Germany), offering high-standard electrical performance and excellent dust and water resistance.
1 of 7Anti-pressure loss cylinder dropping device.
2 of 7Hydraulic Cylinder:
Features high-performance SKF seals and precision machining technology, ensuring outstanding durability and sealing. The surface of the cylinder is hard chrome plated, significantly improving wear resistance, corrosion resistance, and reducing the coefficient of friction, enabling millions of cycles.
3 of 7Guide Rails and Ram:
The guide rails and ram of the metal stamping machine are made of high-strength alloy steel with excellent wear resistance. Employing the most advanced gib-guide technology ensures precise positioning and stable operation with each press.
4 of 7Electronic Control System:
Equipped with a Siemens touch screen and PLC from Germany, offering a user-friendly control experience and comprehensive machine operation monitoring.
5 of 7Workbench:
Customizable workbench, optionally equipped with T-slots, a heating platen, a movable-axis workbench, an automatic ejector cylinder, an exchange workbench, or a shuttle workbench.
6 of 7Pressure Gauge, Temperature Gauge, Flow Meter.
7 of 7Metal Stamping Press Details
- Machine specifications customizable
- High-strength continuous operation
- Pressure range from 10 to 8000 tons
- Processing speed increased by 60%
- International top-tier brand components
- High-quality steel frame
- Siemens touch screen
- Low maintenance
- Lifespan of several decades
- Servo motor saves 50% energy
Hydraulic Stamping Press Structure
The main body of the hydraulic stamping press is a closed-type gib-guided frame, including cross beams, columns, and base, fixed by four tension bolts. The body uses high-quality heavy steel, ensuring high rigidity and minimal deformation, providing excellent parallelism and perpendicularity. This structure is one of the most precise in hydraulic frame types, specifically designed for high strength, high speed, and stable processing.
- Tonnage range from 10 to 8000 tons.
- Workbench area, stroke, tonnage, speed, and pressure are customizable.
- Outstanding parallelism and perpendicularity.
- Servo hydraulic stamping press is 80% quieter than mechanical stamping presses.
- Hydraulic system and tank positioned at the top of the machine to save space.
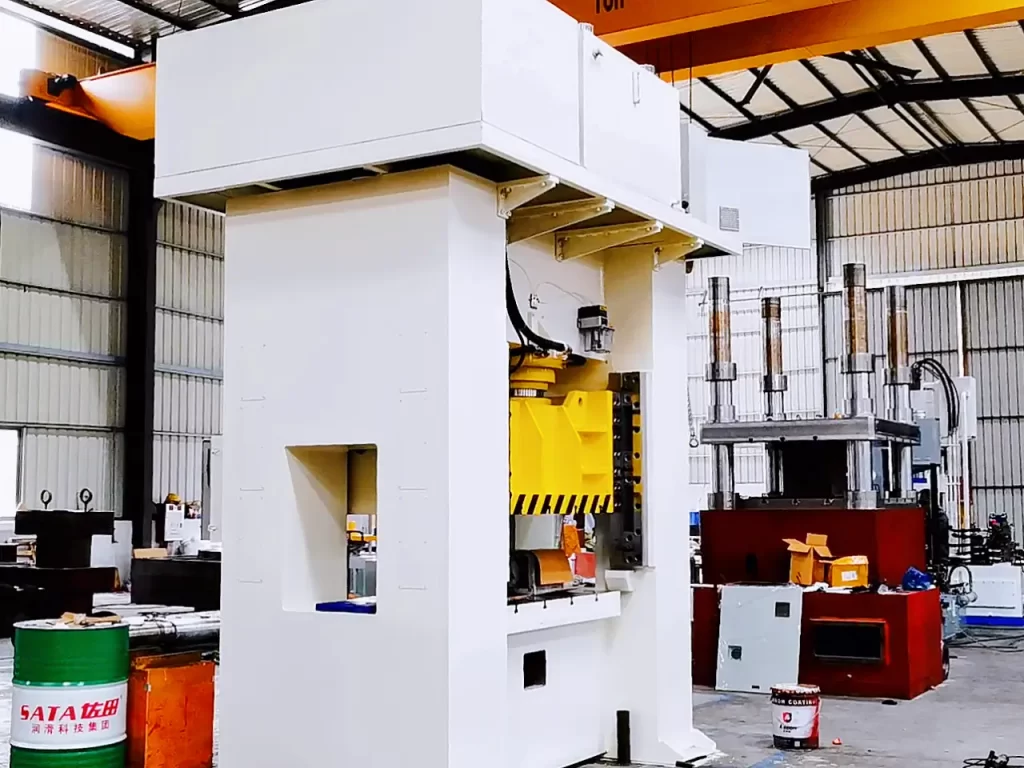
Power and Control Systems
The Lexson series hydraulic stamping press power and control systems are equipped with top international brand components, designed for high reliability and long-term use.
- Equipped with a large, high-definition Siemens control panel. The touch screen panel is clear and intuitive, with recipe functionality.
- Equipped with Italian PHYSIS servo motors, offering quieter operation and 50% energy savings compared to standard motors.
- Equipped with a German Bosch Rexroth modular hydraulic valve group for greater flexibility and lower maintenance costs.
- Equipped with Italian GEFRAN pressure sensors, achieving precision up to 0.1% FS.
- Equipped with a Chinese INOVANCE servo drive, leading the industry in energy efficiency and control capability.
- Power and control systems form a closed-loop control, featuring strong anti-interference, anti-vibration, high integration, and minimizing the risk of oil leaks.
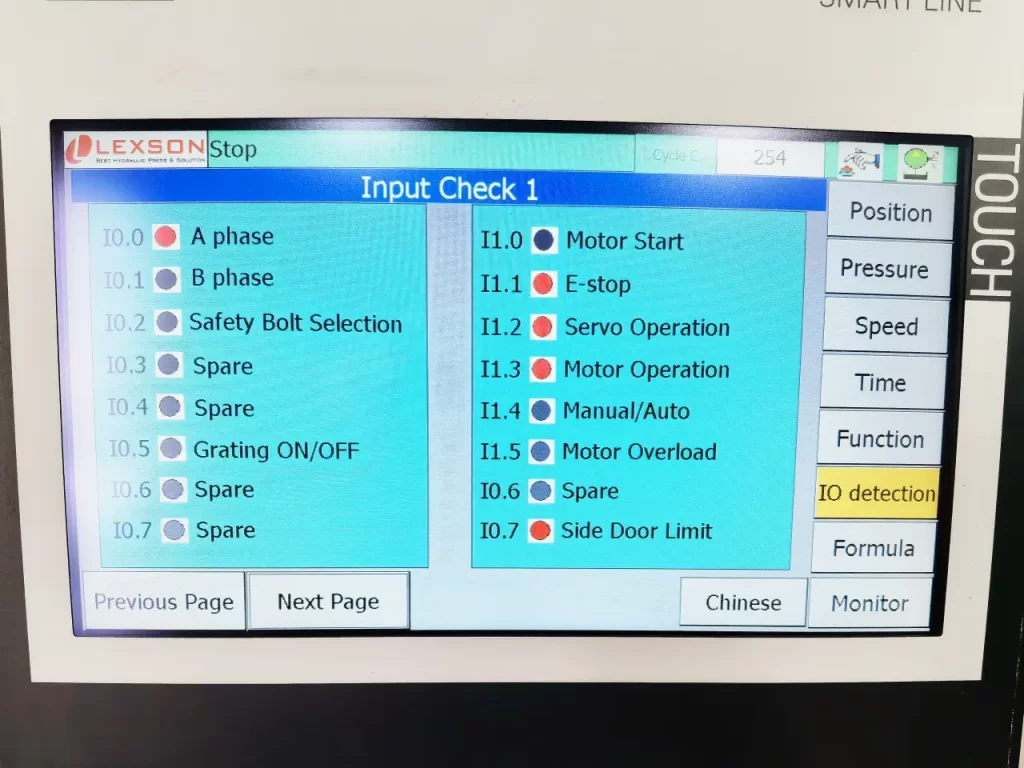
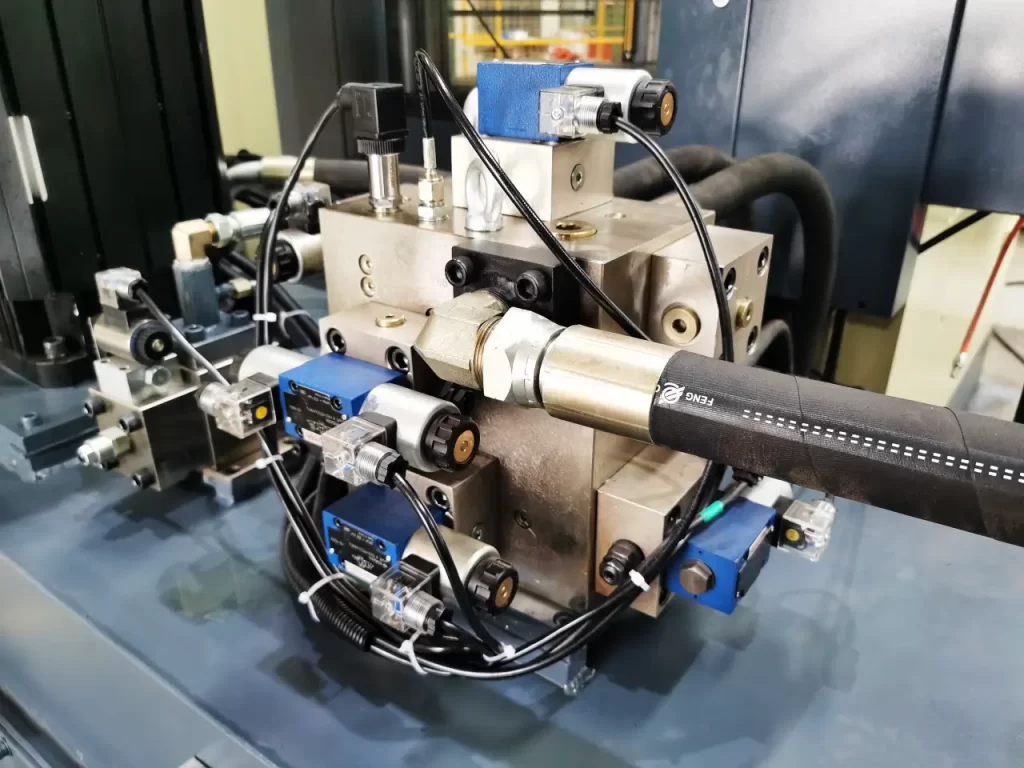
Guide Rails
Our hydraulic stamping press’s guide rail system adopts a line guidance structure. It consists of two upright guide rails and a beam connected at the top. The ram moves precisely vertically along the guides.
- Equipped with an automatic lubrication system.
- Guide rails made of high-strength alloy steel, providing excellent wear resistance and load-bearing capacity.
- Significantly reduces maintenance requirements.
- Significantly distributes the load, reducing body friction and extending machine life.
- Significantly reduces die wear.
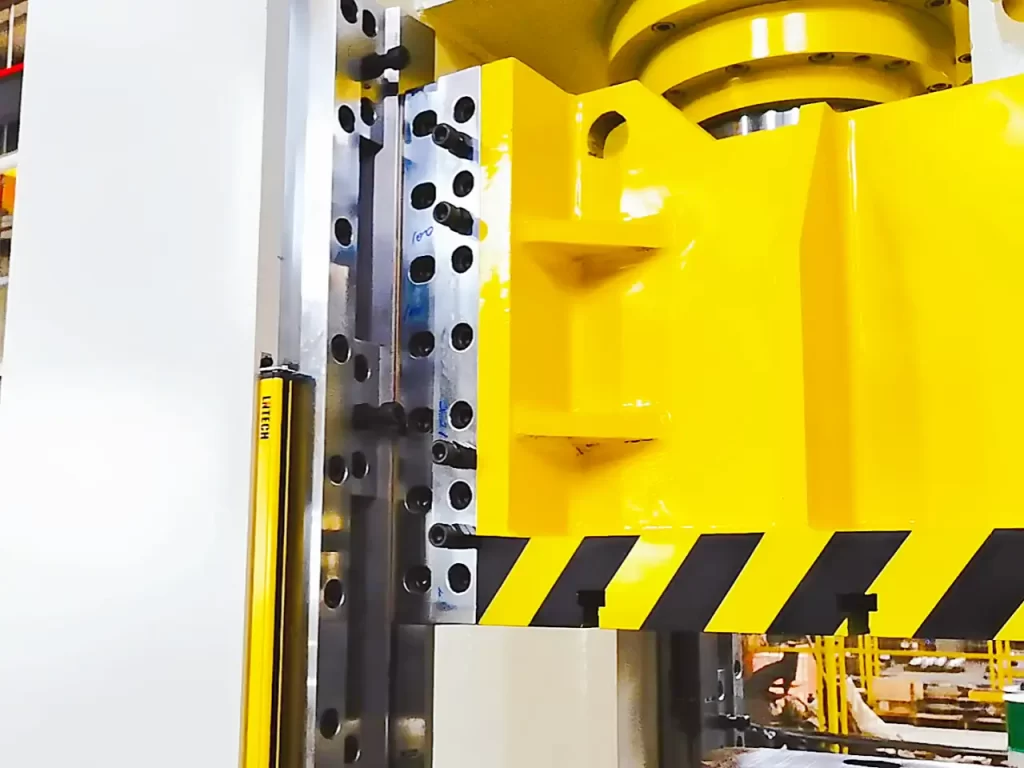
Workbench
The Lexson series hydraulic stamping press can be equipped with various types of workbenches to meet diverse needs.
- Optional T-slots.
- Optional heating platen.
- Optional movable workbench along X, Y, R axes.
- Optional automatic ejector cylinder.
- Optional automated workpiece loading and unloading.
- Optional exchange workbench or shuttle workbench.
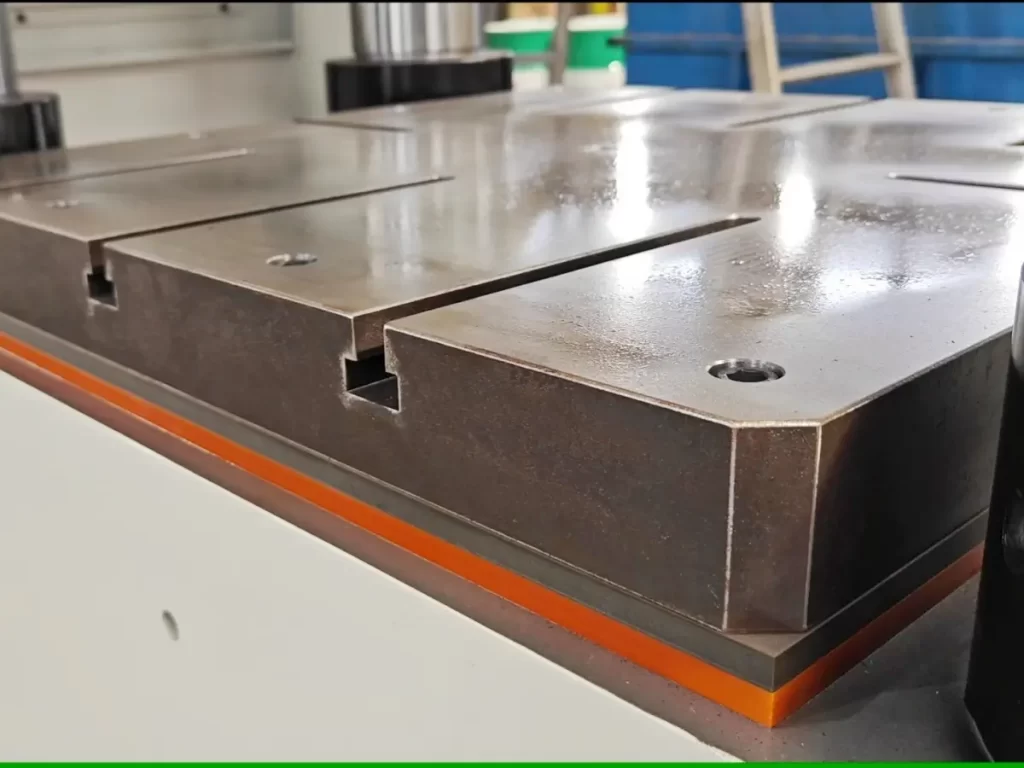
Safety Systems
Hydraulic stamping presses are equipped with safety systems that meet global safety standards. Lexson series presses are built with a no-expense-spared approach to safety, ensuring decades of operation without major accidents.
- CAT4 safety light curtains with dual-channel monitoring.
- Optional pneumatic safety guards.
- Overload protection, pressure loss protection, and drop cylinder protection.
- Equipped with pressure relays, overflow valves, safety valves, and limit switches.
- Dual-hand start buttons and emergency stop buttons.
- Electronic monitoring system that fully monitors pressure, temperature, flow, and other information, recording all operation data.
- Oil temperature sensor and hydraulic oil cooler work together, equipped with an emergency cooling system.
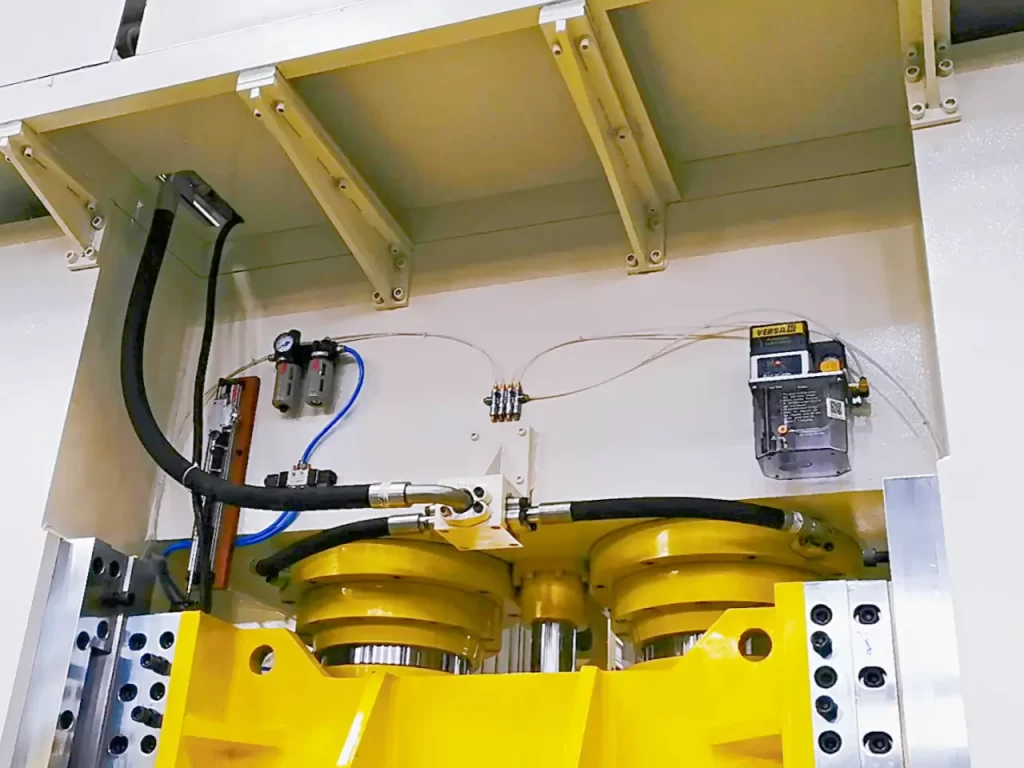
Electrical System
The electrical system of the hydraulic stamping press primarily comes from Schneider (France) and Siemens (Germany). Equipped with a high-standard NEMA electrical cabinet.
- Equipped with a German SIEMENS PLC.
- Equipped with an electrical system cooling device.
- Equipped with circuit breakers, contactors, and relays, these devices protect the electrical system from current overload, short circuits, and voltage fluctuations.
- Equipped with network communication modules for remote monitoring and diagnostics.
- Highest industry standards for wiring and interfaces, anti-interference, moisture-proof, and corrosion-resistant.
- Provision for robotic system integration.
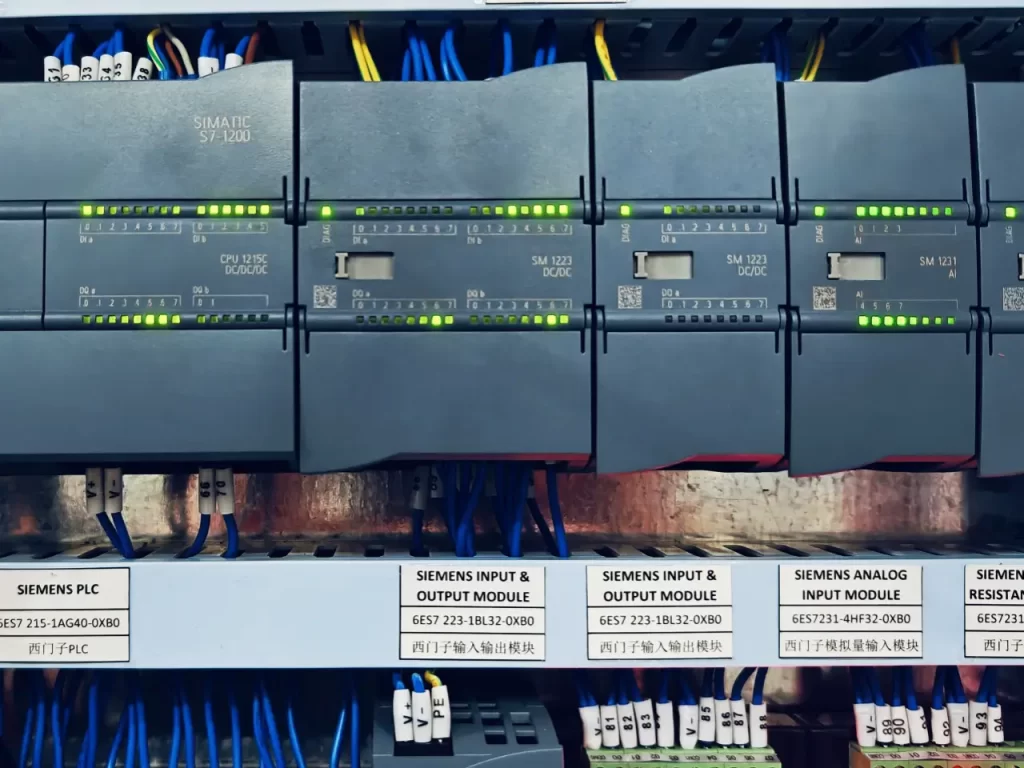
Chase Davis –
Great value for money! This staming press performs as well as other more expensive brands we’ve used in the past.
Noah Klein –
They helped us through the setup process and have been quick to respond to any queries.
Cody Hill –
Very pleased with the energy efficiency of this machine.
Brett Robinson –
We noticed an improvement in our product finish quality almost immediately after switching to this stamping press.
Parker Walker –
The safety features on this press are top-notch. It gives us peace of mind knowing that our operators are safe while working.
Hudson Lopez –
This hydraulic press has exceeded our expectations. It’s robust and reliable, perfect for our stamping needs.
Grant Turner –
Very pleased with the energy efficiency of this machine.
Carter Ford –
The precision control is fantastic. It allows us to produce complex parts with great accuracy.
Reed Carter –
The hydraulic stamping press’s user interface is intuitive and user-friendly. Even our less experienced operators can use it effectively.