Hydraulic Trimming Press
Our trimming press is driven by a servo motor and is equipped with world-class components. Advanced control algorithms ensure fast and precise processing, significantly reducing the scrap rate and ensuring high-quality, burr-free trimming results.
Video

Lexson Series Trimming Press Detail
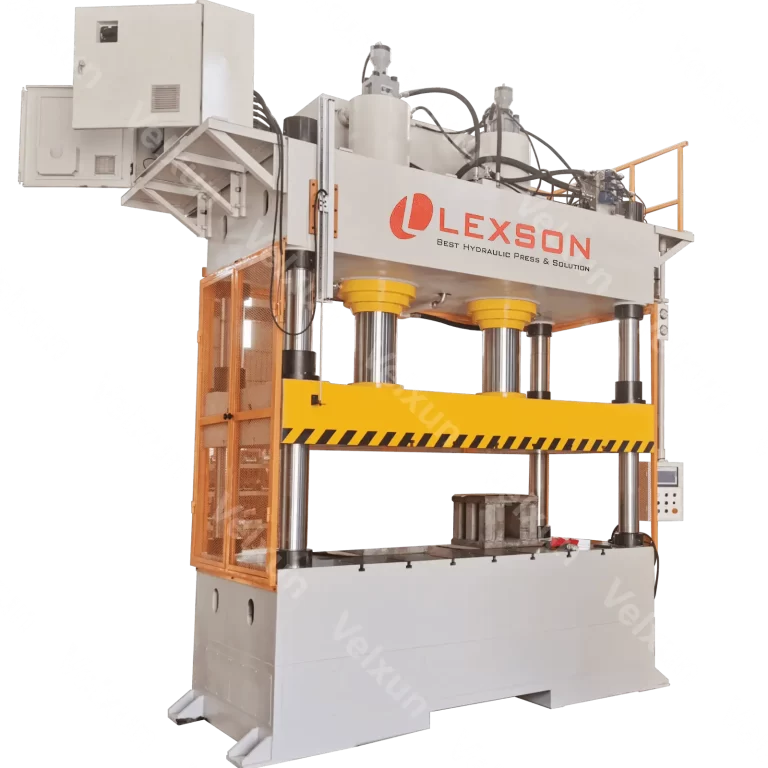
Hydraulic Cylinder:
The main cylinder of the trimming press is made of high-quality alloy, polished, and hard chrome plated. It uses sealing rings from Austria’s SKF, ensuring excellent sealing performance. The design of the main cylinder has a service life of up to 800,000 cycles.
1 of 6Safety Guards:
The hydraulic press can be equipped with metal guards on all four sides that comply with CE standards, and you also have the option to choose a front-mounted pneumatic metal guard, which further enhances production safety.
2 of 6Siemens HMI:
Our trimming press is equipped with Siemens touchscreen and PLC, along with a pressing algorithm optimized for the trimming press. It is easy to learn and offers powerful functionality.
3 of 6Linear Displacement Sensors:
GIVI’s linear displacement sensors from Italy boast an impressive accuracy of ±0.005mm, seamlessly integrating into hydraulic, electrical, and control systems to guarantee an impeccable quality rate.
4 of 6Hydraulic System:
Our trimming press integrates a hydraulic system featuring top-tier international brands. The hydraulic valves are sourced from Germany’s BOSCH REXROTH, the hydraulic pumps come from Germany’s ECKERLE, and the servo motors are supplied by Italy’s PHYSIS.
5 of 6Electrical system:
The Lexson series of trimming presses utilizes electrical components from Schneider Electric, a French company, compliant with NEMA standards, providing stable and reliable performance. It is equipped with overload protection, arc flash prevention, and touch protection.
6 of 6Machine Main Features
- 10 to 1500 tons of pressure.
- Servo-driven, production speed increased by 30%.
- Machine noise reduced by 50%.
- Industry-specific machinery, highly customized.
- 20% of the heat compared to a traditional hydraulic press.
- Machine energy consumption reduced by 50-70%.
- Positioning accuracy ±0.01mm.
- Pressure error ±1 bar.
- Closed-loop system for real-time monitoring to achieve burr-free trimming.
- Linear displacement sensors accuray up to ±0.005mm.
- Robust security system.
- World-class components.
Additional services
Offering customized solutions for trimming presses.
Integratable automatic feeding system, integratable robotic arm.
Providing comprehensive trimming die solutions.
Trimming Press Structure
Our hydraulic trimming press has a modern appearance and compact four-column design for convenient loading and unloading of dies or tools. The frame is made through integral welding process, with a small footprint. The machine body undergoes heat treatment, sandblasting, and shot blasting processes. The spacious worktable and long stroke are suitable for accommodating large workpieces. Dual hydraulic main columns ensure even pressure distribution, guaranteeing smoother cutting edges. Depending on requirements, 2-4-sided metal safety guards can be configured, with optional pneumatic safety guards.
The bed of Lexson’s trimming press series undergoes finite element analysis to ensure minimal deformation under hydraulic pressure. It exhibits surface fatigue resistance, resistance to alternating loads, and wear resistance, making it suitable for continuous operation under high-temperature conditions.
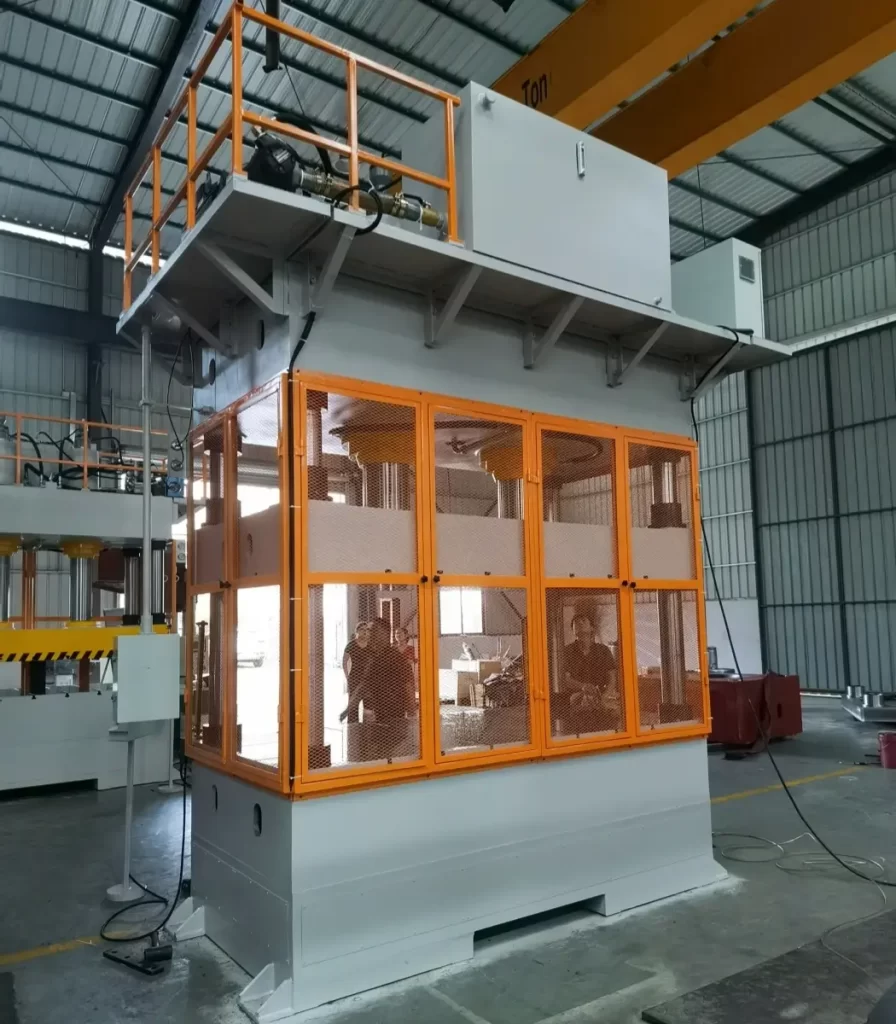
Permanent Magnet Synchronous Servo Motor
Our trimming press utilizes the permanent magnet synchronous servo motor imported from Italy by PHYSIS, saving 50% of electricity, reducing noise by 50%, and generating lower heat. Servo motors have become the industry’s preferred choice, adjusting energy consumption based on demand during operation. In our long-term validation, it has demonstrated superior control performance and stability, ensuring that the trimming press can operate under high loads for extended periods.
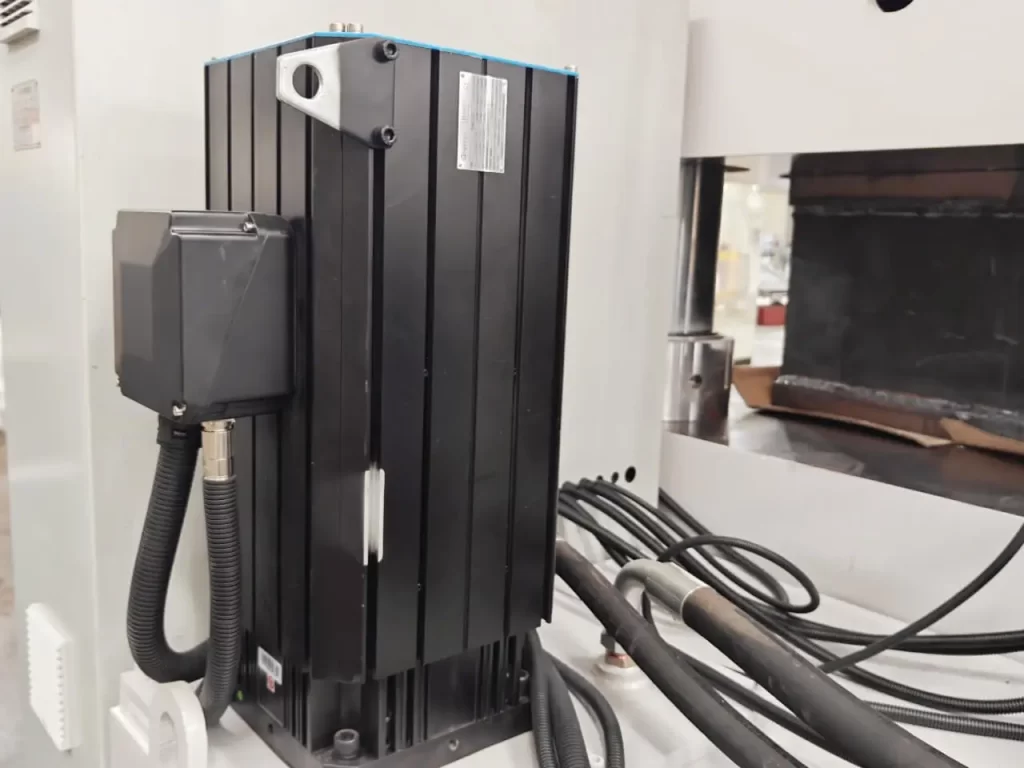
Control System
The Lexson series trimming press is equipped with Siemens PLC and a high-definition touchscreen from Germany, along with servo drives from the high-end Chinese brand Inovance. It features optimized pressing algorithms designed specifically for trimming presses, ensuring more even force distribution during cutting or edge removal, resulting in precise and smooth trimming.
- 10-inch high-definition color screen.
- The control system integrates with the hydraulic system, electrical system, various monitoring devices, and sensors to form a closed-loop control.
- Multiple program storage options, capable of storing tens of thousands of programs.
- Provision for robot interface.
- The control system is specially optimized for various trimming press applications.
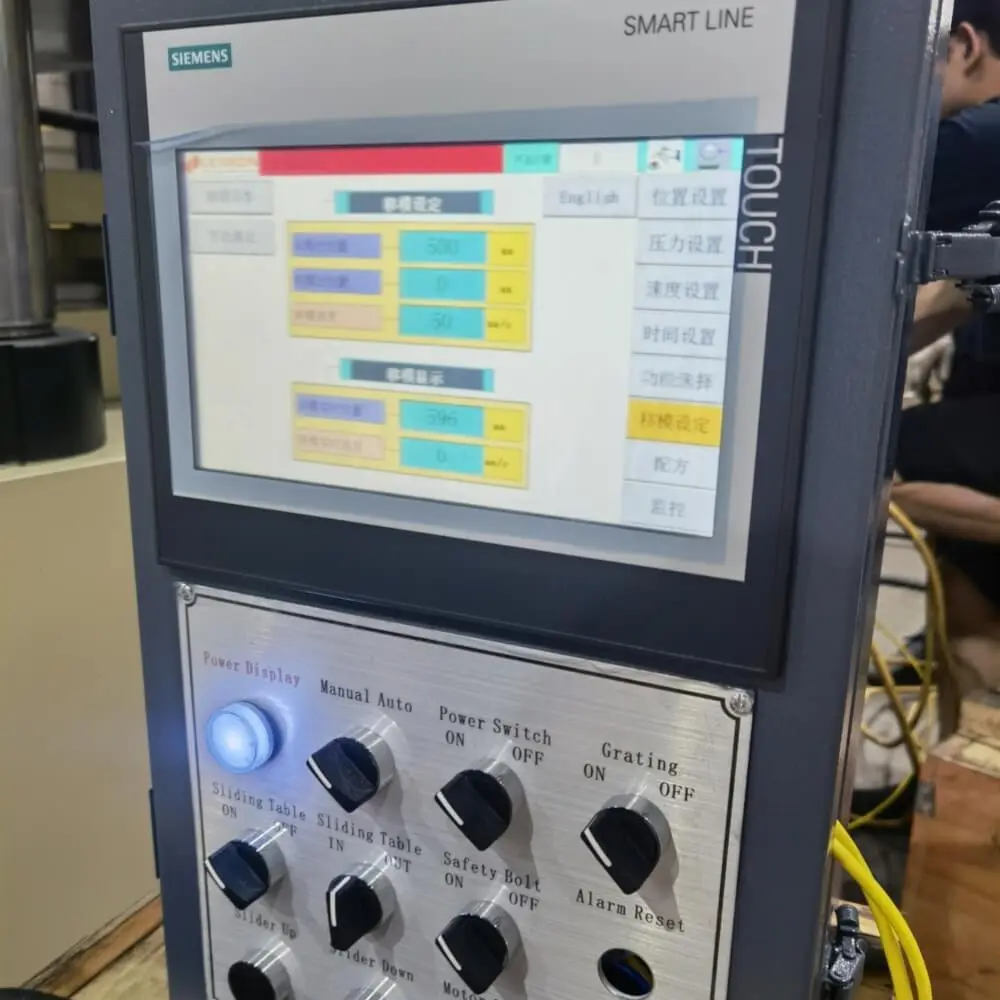
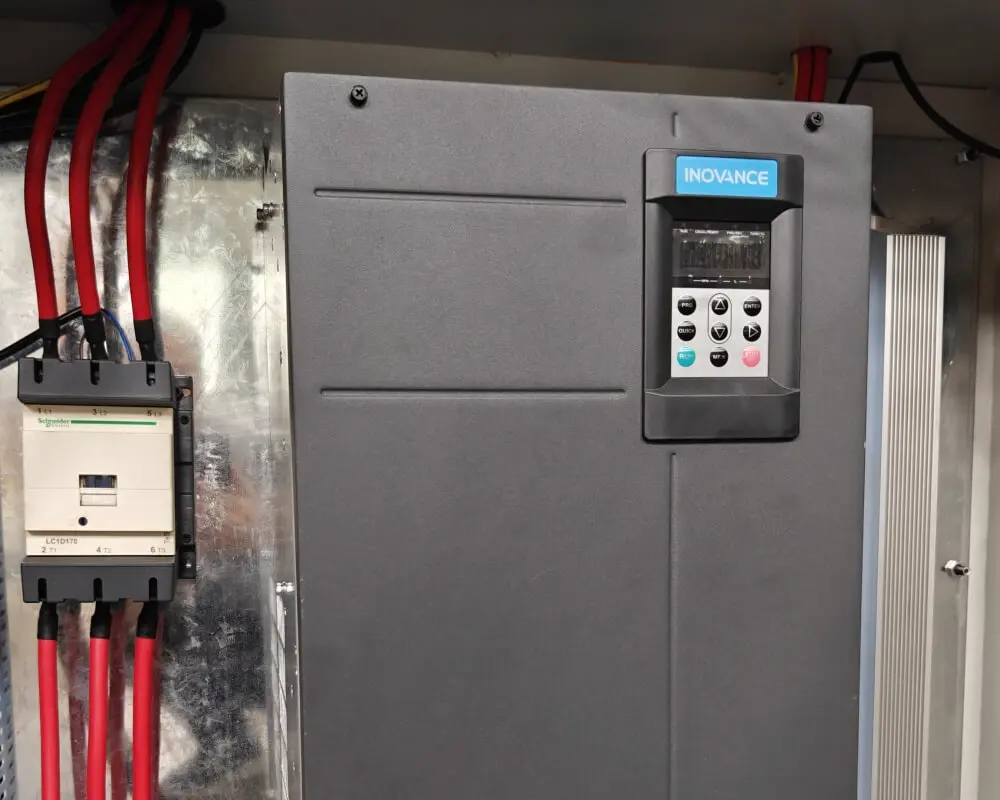
T-Slots
The ram and worktable of Lexson series hydraulic trimming presses are both equipped with T-slots for the installation of dies. The body is made of high-quality wear-resistant materials, serving not only as a working platform but also as a cornerstone for precision machining. Their outstanding parallelism and premium materials allow them to maintain long-lasting and reliable operation even under high loads.
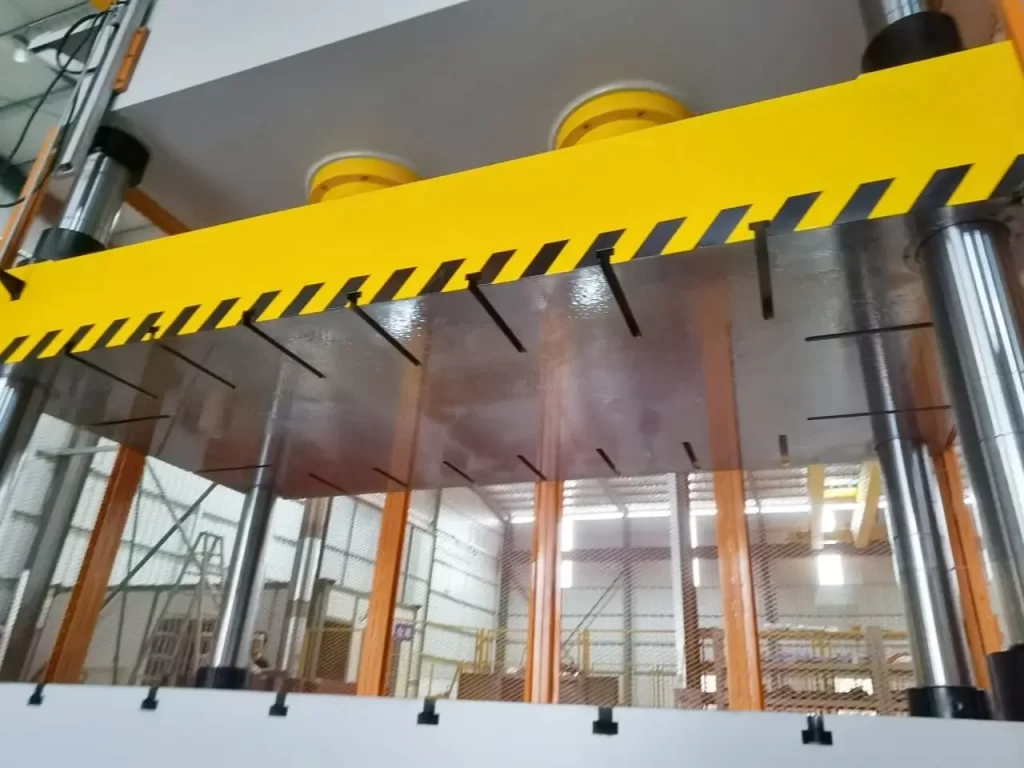
Hydraulic System
Our hydraulic trimming press’s hydraulic system primarily originates from Germany. It comprises a quiet hydraulic pump, hydraulic valves, a water-cooled heat exchanger, pressure gauge, oil tank, oil filters, and air filters, among other components. It provides precise control and long-term stable performance. With a modular design and minimal piping, it significantly reduces the possibility of oil leakage.
- Specially designed to prevent oil leaks and insensitive to oil contamination.
- Equipped with a water-cooled heat exchanger.
- Hydraulic valve groups from Bosch Rexroth in Germany.
- Hydraulic seals from SKF in Austria, offering excellent sealing and durability.
- Hydraulic pumps from ECKERLE in Germany, known for their quiet operation and precise control.
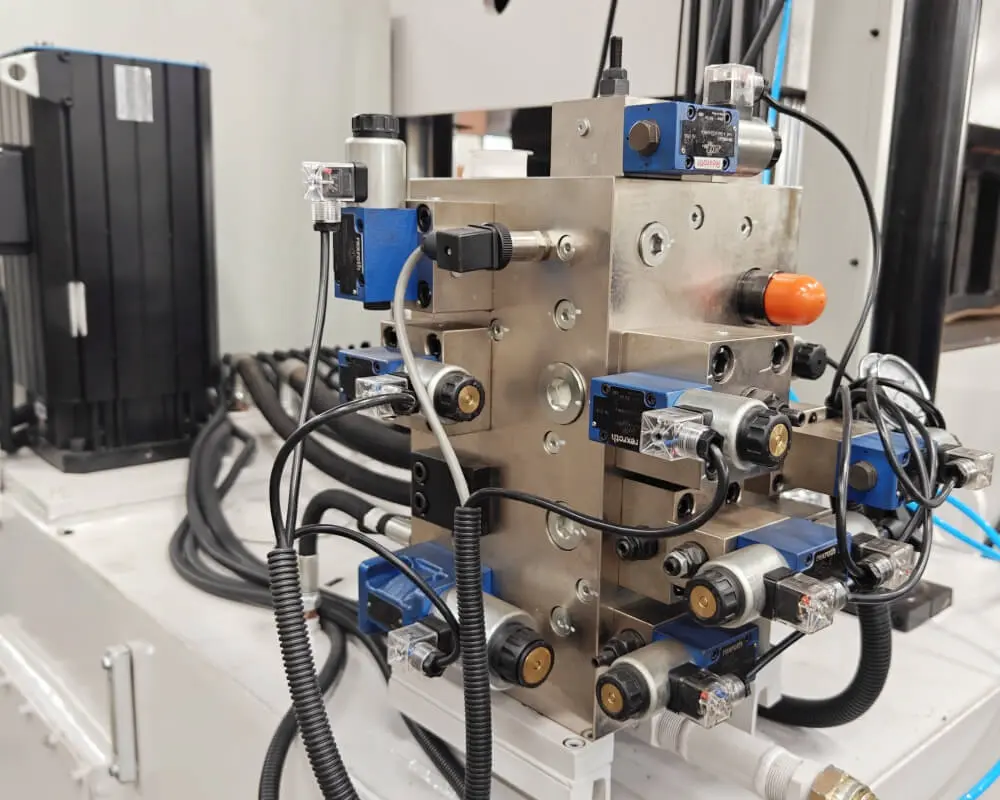
Electrical Cabinet
The Lexson series trimming press is equipped with electrical components from Schneider Electric in France, ensuring excellent stability and safety.
- NEMA-style electrical cabinet.
- Cabinet door interlock switch.
- Two debris-resistant cooling fans (inlet and outlet).
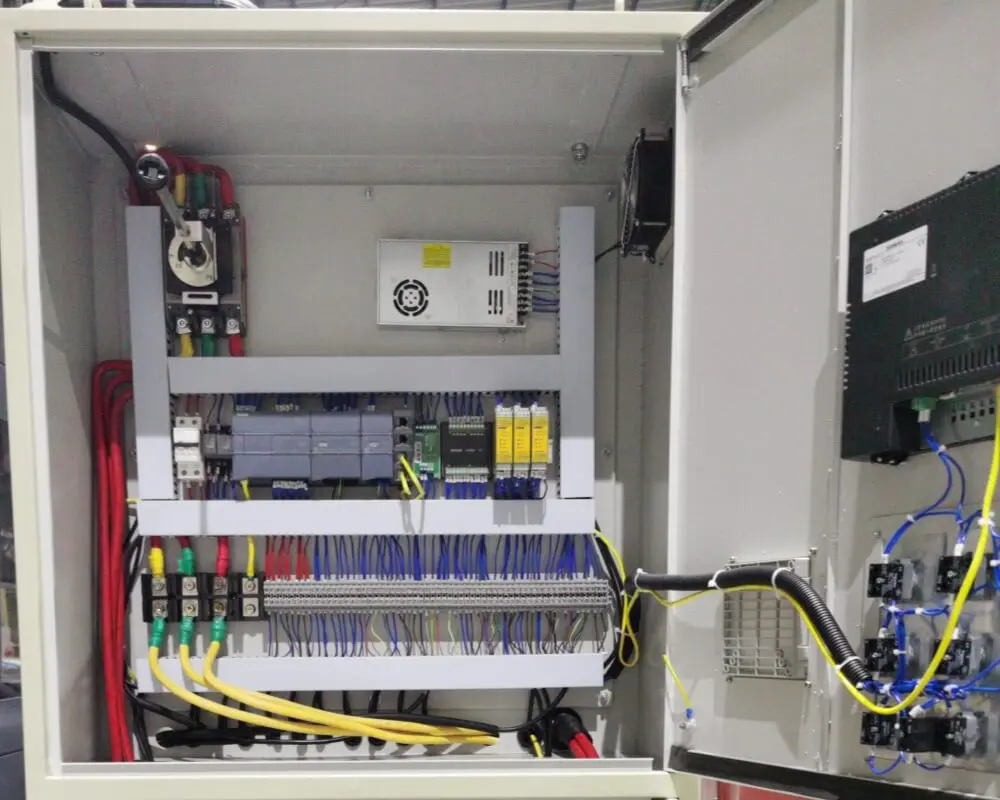
Monitoring and Sensors
Here is a partial list of monitoring and sensor components for our trimming press, ensuring proper feedback and adjustments during edge cutting.
- GIVI linear displacement sensors from Italy.
- GEFRAN pressure feedback sensors from Italy.
- SMC pressure regulators from Japan.
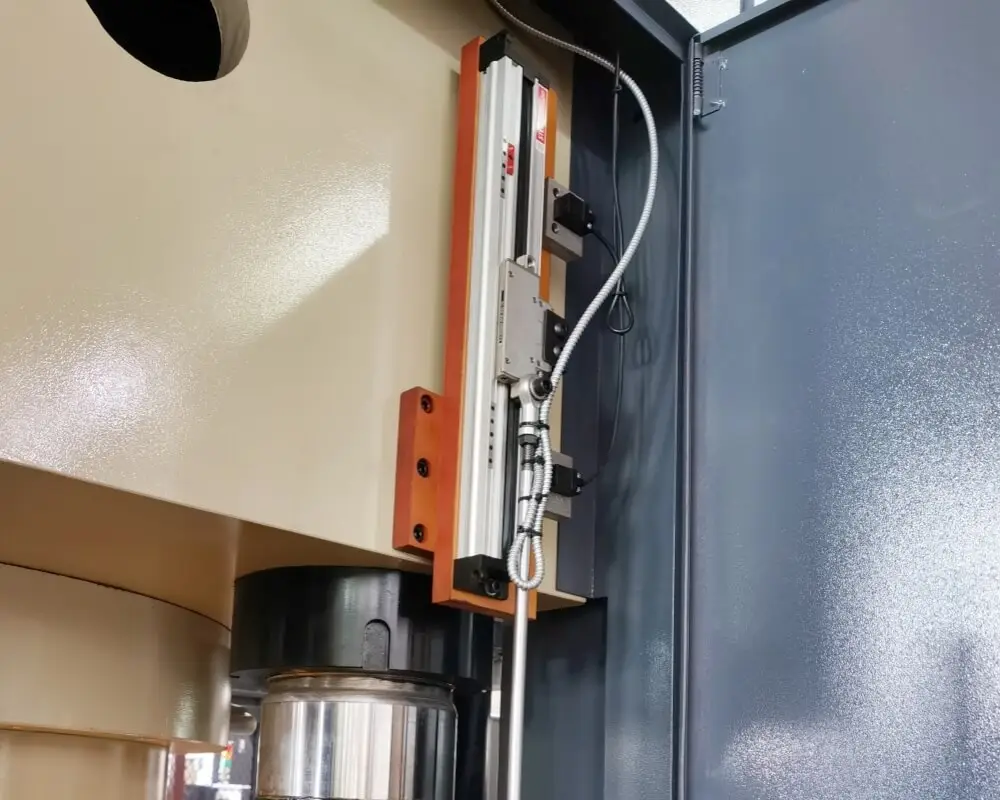
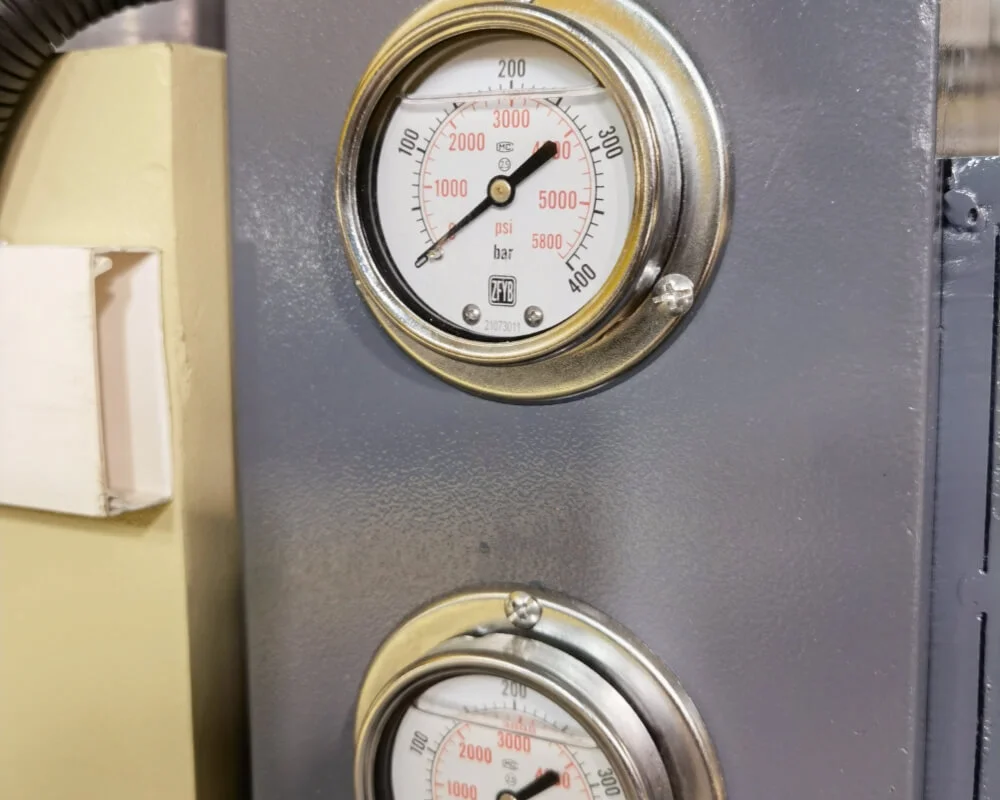
Safety Measures
Our Trimming press is equipped with a safety light curtain, covering the entry and exit points of the workpiece, with the option to add mechanical safety sensor for further safety guards. The metal safety guard meets the CE standard and is perforated with a mesh design to facilitate observation of the workpiece processing. We are well-versed in the export standards of multiple countries and can customize your trimming press safety system based on the safety standards of different regions and countries.
- CE standard metal safety guards, with the option of pneumatic safety guards.
- Enhance machine safety by incorporating locking cylinders from SMC(Japan).
- Two-hand start buttons, with the option of American Banner optical buttons.
- Emergency stop buttons located at the front and rear of the machine.
- Tricolor indication lights (green/yellow/red) and a buzzer indicate safe operations.
- Safety light curtains covering the feeding area, compliant with CAT4 standards.
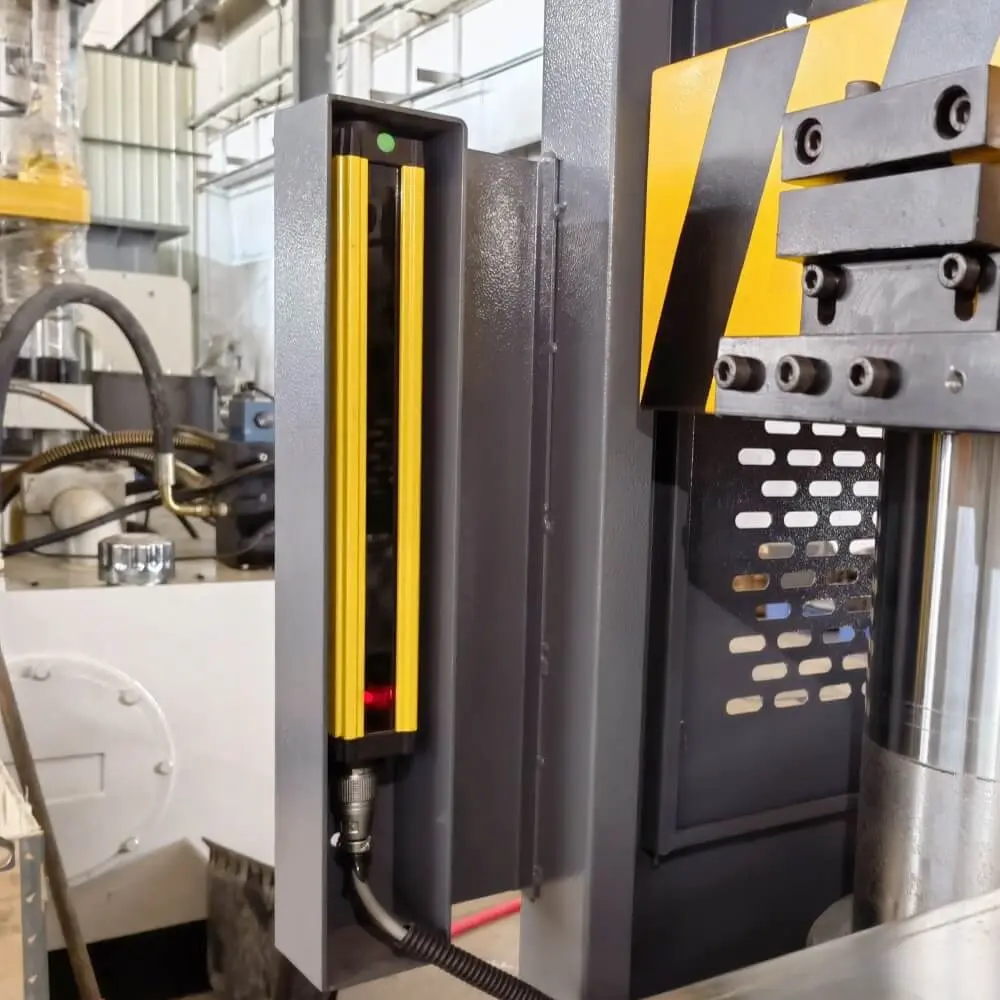
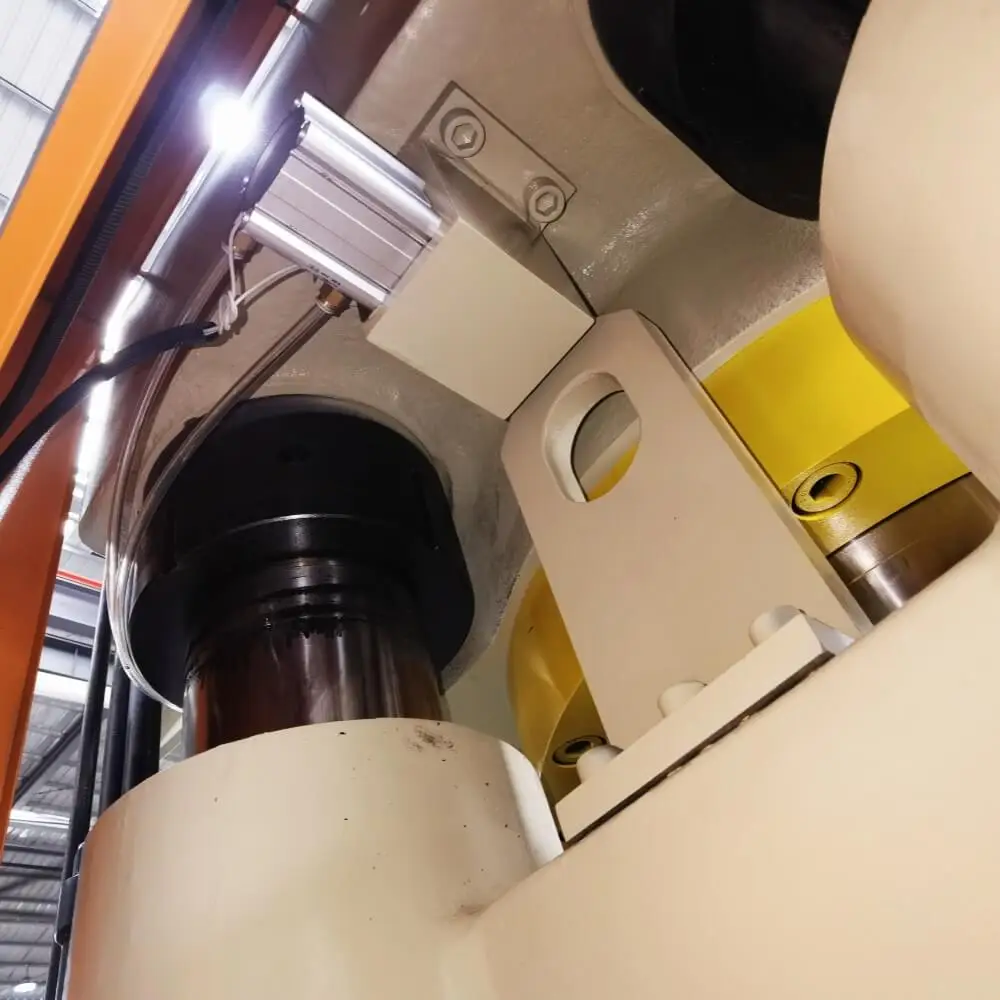
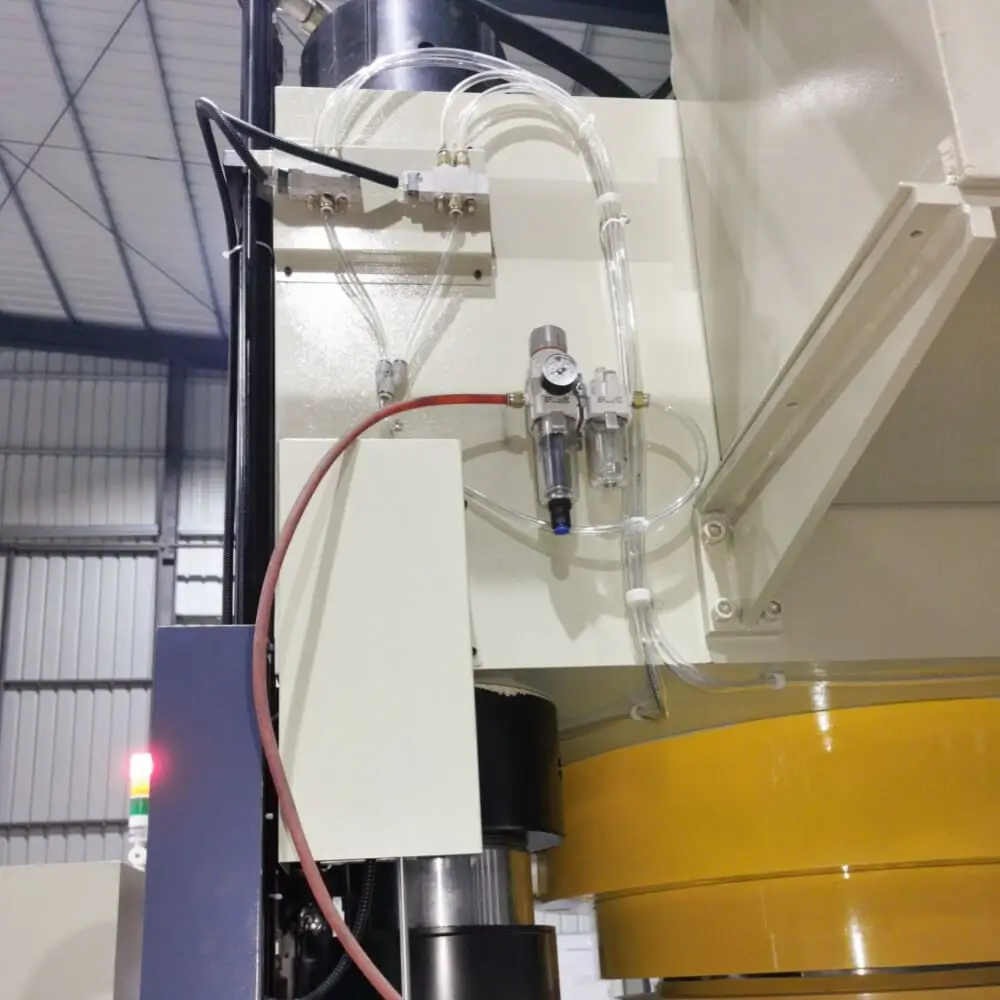
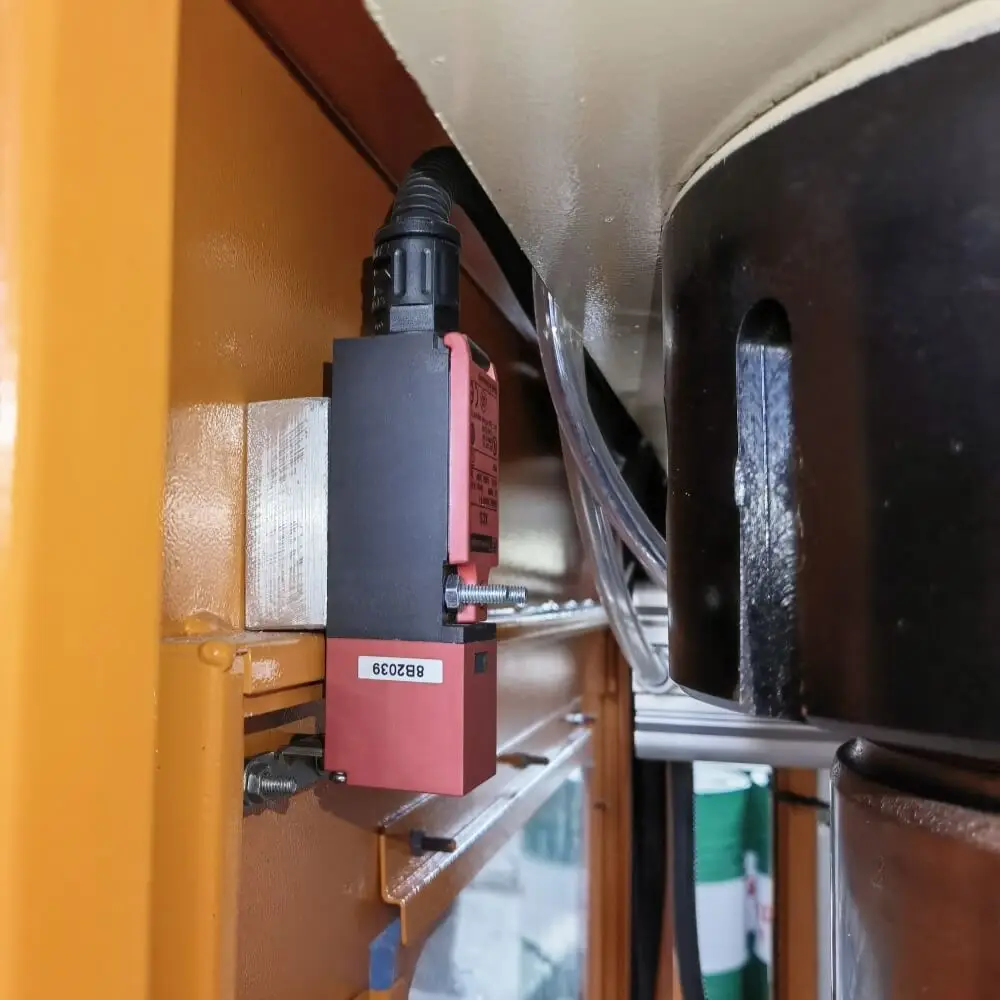
FAQ
What is a trimming press?
Trimming Press is an industrial machine used in manufacturing to cut, stamp, or trim materials such as metal die castings, plastic, rubber, and more. It typically applies high pressure between the dies and the workpiece using hydraulic power to trim and flatten any excess edges on the workpiece.
What is the price of a trimming press?
The price of our trimming press varies significantly based on different configuration requirements. We offer multiple options to choose from. For more details and to obtain the most competitive price, please click the button below.
What are the application areas of trimming presses?
The trimming press can be used for various types of metal die-castings, plastics, foam, rubber, etc., covering industries such as electronics, aerospace, automotive, and construction. It is most commonly employed for die-castings made of aluminum, magnesium, and zinc materials.
What are the advantages of your trimming press? Why should I choose your products?
- We are a hydraulic press manufacturer at the source, with a complete industry chain layout, making us more competitively priced.
- Our strict quality control ensures that each machine undergoes a rigorous one-week testing process before leaving the factory.
- We have accumulated over thirty years of experience in the hydraulic press industry.
- Each of our hydraulic presses is specially optimized for specific industry applications and undergoes extensive validation as a mature product. For example, the control system and pressing algorithms of this trimming press have been specially fine-tuned, making it a true industry-specific machine.
- Our pre-sales and after-sales services are mature, with rapid response times, and we provide global maintenance services.
- Our machines can meet your customization needs, providing comprehensive and tailored solutions from all angles.
How long does machine production take?
Based on the specific requirements, machine production typically takes about 3-6 weeks from order confirmation to machine completion and testing.
What type of heat exchanger is provided, and how is the temperature controlled?
We use a water-cooled heat exchanger. Cold water circulates inside the heat exchanger, while heated oil flows through the oil channel within the exchanger. The water removes heat from the oil.