The History of Jigsaw Puzzle
Origin
The first jigsaw puzzle originated in London, England, in the year 1760. It was the brainchild of a geographical educator who came up with the idea quite unintentionally. He divided a world map into pieces to be used in geography education. This innovative approach not only enhanced memory retention but also fostered visual-spatial reasoning skills. This marked the creation of a universally enjoyable and enduring puzzle game.
Evolution of Puzzle Manufacturing
During the mid-18th century, the earliest jigsaw puzzle production involved using a saw to cut wooden boards into individual pieces, which were then polished. At this stage, the puzzles were quite rudimentary, and each piece was unique.
In the early 19th century, people began using mechanical saws to assist in cutting, leading to an increase in production efficiency. In the later part of the 19th century, with advancements in printing technology, the rise of paper puzzles gained momentum. This was due to paperboard material being lighter, more cost-effective, and suitable for printing intricate designs, thereby enhancing both the playability and artistic value of puzzles. Concurrently, the rudiments of die-cutting technology also began to take shape.
In the 20th century, as printing and precision cutting technologies further evolved, paperboard puzzles became commonplace and more exquisite, with the patterns on each puzzle piece becoming more vibrant. Die-cutting technology also saw rapid development.
In the 21st century, with the development of computer technology and the rise of CNC (computer numerical control) manufacturing, various types of CNC machinery became mainstream. Customized puzzle production became more straightforward, leading to the emergence of diverse puzzle categories such as 3D puzzles, new materials puzzles, double-sided puzzles, and custom image puzzles.
In 2019, the outbreak of the COVID-19 virus led to widespread home isolation measures in many countries, triggering a surge in jigsaw puzzle sales. Additionally, due to changes in people’s habits following the pandemic, jigsaw puzzles continued to maintain higher sales than before. Many factories underwent automation upgrades due to the pandemic’s impact.
Today, world-class puzzle factories have already embraced intelligent and automated systems, achieving fully automated production lines. With the diversification of materials used in puzzle production, many smart factories have customized production lines tailored to their specific needs.
Jigsaw Puzzle Production Process
Design and Printing
The images on jigsaw puzzles are typically designed by designers, purchased as copyrighted images, or even generated using AI. Currently, there’s a trend of AI-generated puzzle images, which not only avoids copyright issues but also produces stunning visuals, thereby reducing costs and increasing efficiency.
Most jigsaw puzzle manufacturers use lithographic printing technology to imprint puzzle patterns onto paperboard. It is a process in which oil-based paint is transferred onto the paperboard through a rotary printing method. This method is cost-effective and suitable for large-scale production. Another emerging method is laser printing, which has become a trending choice. This method offers greater flexibility but comes with a slightly higher cost.
Automatic Lamination
The Automatic Lamination Machine is used in the coating process, applying one or multiple layers of protective coating onto the printed design of the puzzle. This enhances the puzzle’s surface hydrophobicity and durability, ensuring long-lasting use without fading or corrosion. Following this, hot foiling is performed using either high-gloss or matte foil, adding texture and aesthetic appeal to the puzzle.
Next, the printed puzzle image will undergo adhesive application using the Automatic Lamination Machine, typically utilizing water-based, non-toxic adhesive. Subsequently, it will be bonded to the cardboard. After bonding, the puzzle is usually left to rest for several days until the adhesive is fully cured.
The paperboard used in puzzle factories is generally purchased externally, and some high-quality puzzle factories require specially customized paper. Common types of paperboard include Blue Core Paper, Greyboard, and wood-based materials.
- Blue Core Paper: In comparison to other paper types, Blue Core Paper is considered healthier and more environmentally friendly. It offers a superior tactile sensation with a softer texture and is less prone to creasing. It’s a primary material used for making puzzles in the European and American regions.
- Greyboard: Greyboard is more affordable, but it tends to have more paper scraps, resulting in an average tactile experience. It’s difficult to restore its shape if it gets creased.
- Wood Board: Wood boards are characterized by their hardness, resistance to deformation, durability, strong interlocking, and relatively higher weight. However, their drawback lies in the tendency to become brittle and the presence of more wood chips. With technological advancements, wood board materials have gradually matured, and there is a trend toward replacing Blue Core Paper.
- Plastic: Plastic offers higher moldability, customizable shapes, waterproof and moisture-resistant properties, durability, and a strong interlocking fit. It’s the optimal material for high-end 3D puzzles but lacks environmental friendliness. Its major drawback is its expensive price, owing to high mass production costs.
Puzzle Cutting
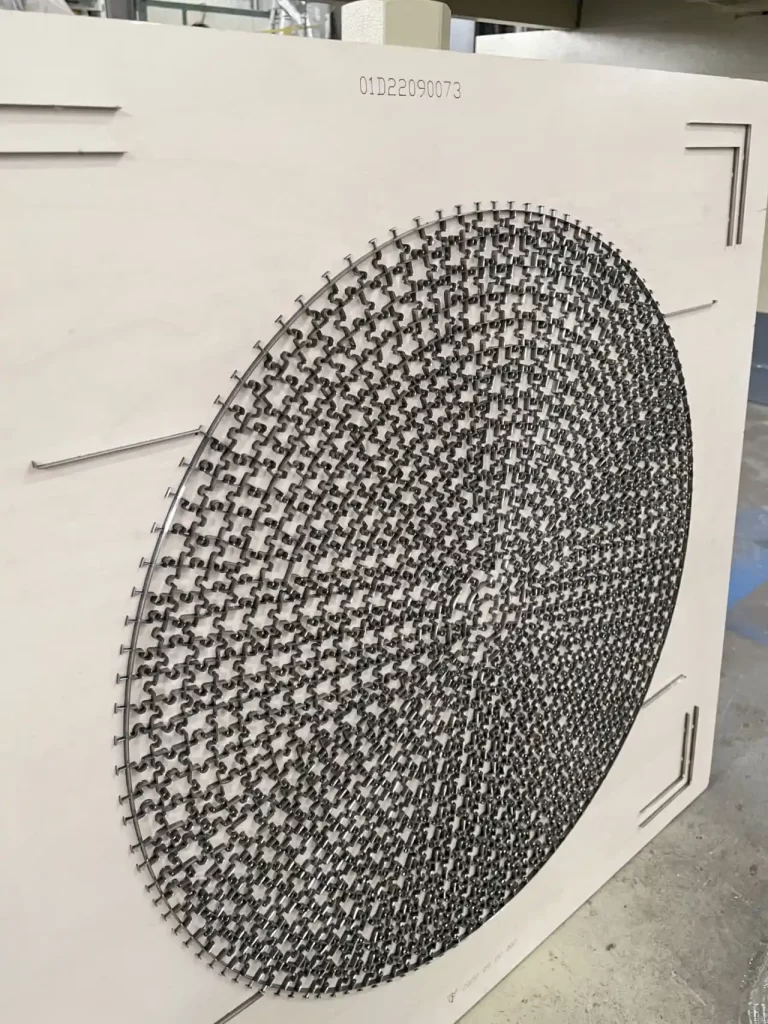
Currently, there are two main approaches: laser cutting and the use of a die cut press.
In the realm of jigsaw puzzle cutting, die cut press machines (such as hydraulic presses) and steel rule dies have become crucial tools for mass production. Laser cutting, due to various limiting factors, is more commonly used as a supplementary production method.
Laser Cutting Method
This is a more advanced approach, offering greater freedom and precision in shaping puzzle pieces through laser cutting. However, its drawbacks are also quite pronounced. The cost is extremely high, and production speed is slow. It’s not cost-effective for large-scale production. Material options may be limited, and it may not be suitable for certain specialized materials.
Die Cutting Method
Using hydraulic presses and steel rule dies, this is a more cost-effective and mature solution. The puzzle die is pressed into the puzzle cardboard using hydraulic pressure, resulting in high production efficiency. One drawback is that when changing the size or shape of the cut, a new puzzle die needs to be customized. The precision is not as exact as laser cutting, but it is entirely sufficient for the jigsaw puzzle industry.
- Hydraulic Press: In the die-cutting process, a four-column hydraulic press is commonly used due to its stable structure, larger worktable area, and higher cost-effectiveness. Typically, a 1000-piece puzzle requires a 700-ton hydraulic press, while a 2000-piece puzzle requires a 1200-ton hydraulic press. The substantial pressure places higher demands on the cutting dies. Notably, Velxun’s subsidiary brand Lexson has gained global recognition for its puzzle making machines, with their intelligent production lines widely adopted in the smart manufacturing processes of the world’s top ten puzzle factories.
- Steel Rule Die: For cutting puzzles, a steel rule die is commonly used. It’s a type of die made by laser-cutting high-strength adhesive plywood and embedding blades into slots. Each slot on the blade is precisely cut by lasers, ensuring accuracy during puzzle cutting. In the hydraulic press process, the blades on the steel rule die are pressed onto the prepared puzzle cardboard. Once the pressing is complete, the die ejection rubber on the steel rule die ensures the puzzle pieces are properly ejected and not adhered to the die. Even now, the production of steel rule dies still involves a significant amount of manual work, with each blade needing to be manually inserted into slots. Creating a steel rule die for a 1000-piece puzzle still takes 5-7 working days. Lexson’s puzzle dies leads the industry, boasting top-tier processing techniques, blades, and baseboards, all while maintaining a high cost-performance ratio. A quality die often determines whether the produced puzzles have uniform and clean edges.
Puzzle Scatter Process
After the cutting process is completed, the puzzles are transported to a machine vision inspection device, which checks for any missing pieces. Once the inspection is done, the puzzles are conveyed via a conveyor belt to the puzzle scatter machine. This machine is equipped with silicon rods designed for efficiently and evenly scattering the puzzle pieces at high speed while ensuring the puzzles remain undamaged.
Puzzle Bagging and Packaging
Next, the puzzle will go through the puzzle bagging machine for PE film heat sealing packaging, followed by entering the testing phase conducted by quality control personnel. After passing the inspection, it will be boxed and delivered to consumers’ hands.
Conclusion
The production of jigsaw puzzles involves numerous specialized equipment and expertise, requiring continuous technological accumulation. To stand out in the industry, the intelligent upgrading of production lines is imperative.
Under the umbrella of Velxun Machine, the subsidiary brand Lexson offers a complete range of automated solutions, including puzzle cutting machine, puzzle die (steel rule dies), puzzle scatter machines, puzzle bagging machines, puzzle packaging machines, puzzle lamination machines, box lamination machines, and more, all essential in the puzzle production process. These solutions have been consistently supplied to world-class puzzle manufacturers and are exported to over 40 countries worldwide. If you have any inquiries about puzzle production processes and equipment, please feel free to consult our team of experts.