What is a press brake crowning system?
The crowning system for a press brake is a system used during the bending process to ensure more even distribution of force on the workpiece. Since a press brake is powered by hydraulic cylinders on both the left and right sides, the workpiece experiences higher forces at its ends, with force diminishing towards the center. This uneven pressure distribution leads to inconsistent bending angles, with smaller angles occurring in the central region of the workpiece.
To address this issue, the worktable applies a counteracting force to the workpiece, ensuring that it experiences even pressure from the left, center, and right sides. This ensures consistency in the bending angles of the workpiece and significantly reduces deformation.
This is the reason behind and the working principle of the crowning system in a press brake. Nowadays, it is commonly found in larger tonnage press brakes, with the demand for it increasing as the tonnage gets higher.
Currently, there are primarily two methods in use: hydraulic crowning and mechanical crowning. These methods are applied in real-time during the machining process and do not impact production efficiency. Nowadays, upgrading this configuration is no longer expensive. We can significantly improve the precision and yield of machined components with a small investment.
What are the differences between hydraulic and mechanical crowning?
What is Hydraulic Crowning for Press Brake?
Hydraulic crowning in press brakes began to be used in the 1960s. It utilizes hydraulic power and the elasticity of the steel plate, with multiple small hydraulic cylinders (usually 1-7 cylinders) pushing in the opposite direction. In the 1980s, complex closed-loop control hydraulic crowning systems were developed. CNC systems control the forces of these small hydraulic cylinders independently, dynamically applying compensation pressure to ensure consistent bending angles.
It is typically installed beneath the worktable, with the number of hydraulic cylinders determined by the length of the worktable. Typically, the longer the worktable, the more compensation hydraulic cylinders are required.
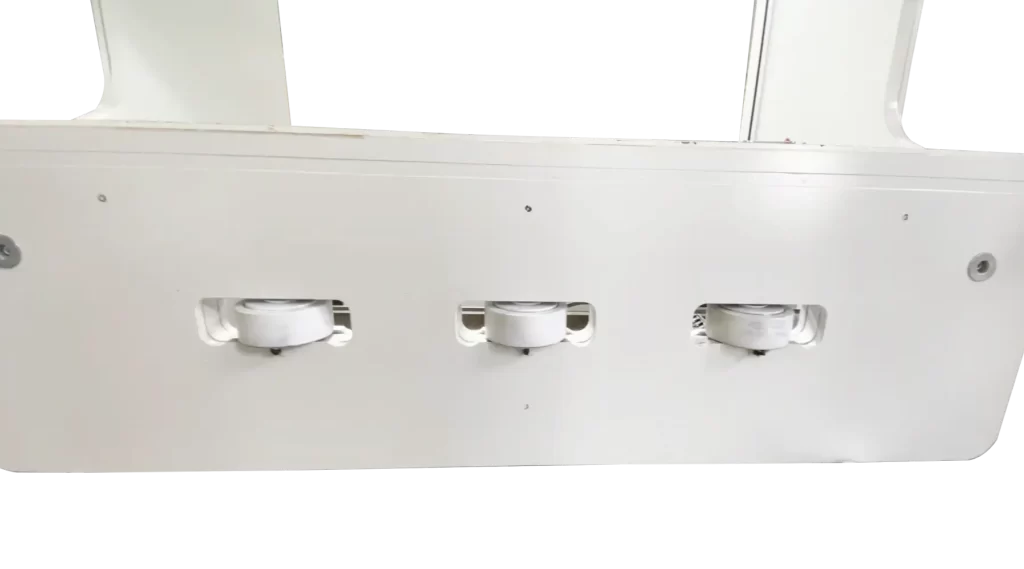
Characteristics of Hydraulic Crowning
- Operator Skill Requirements: Simple operation, no manual intervention required. Low technical skill requirements for workers, who can effortlessly achieve the desired results.
- Precision: In the case of workpieces involving multi-step bending, the real-time adjustment capability of hydraulic crowning results in higher precision and a better effect on compensating for metal springback. It can independently adjust for each step to adapt to different bending processes. For shorter workpieces, there is little difference between the two methods, but the accuracy of hydraulic crowning may be slightly lower for longer workpieces due to the presence of a compensation blind spot, as there are typically 1-7 small hydraulic cylinders.
- Maintenance: Due to the use of hydraulic systems, there is a risk of oil leakage. Regular inspections and the replacement of pipelines and seals are necessary, which can lead to additional costs.
- Applicability: Suitable for most bending scenarios, especially well-suited for workpieces involving multi-step bending processes. However, there are limitations to the processing accuracy of long or large workpieces.
- Price: Hydraulic crowning systems typically have slightly higher costs due to the need for oil pumps, hydraulic circuits, seals, and monitoring systems, but the overall difference is not substantial.
What is mechanical crowning for press brake?
Mechanical crowning in a press brake, which was first applied in the 1950s, is one of the earliest compensation methods. It uses an electric motor to drive a distributed set of protruding wedge components located beneath the die. These wedges create a counteracting force on the workpiece. Mechanical crowning can be applied at any position beneath the die and has numerous contact points. Therefore, its precision advantages become increasingly evident as the length of the workpiece extends. It can significantly reduce the issue of inconsistent bending angles.
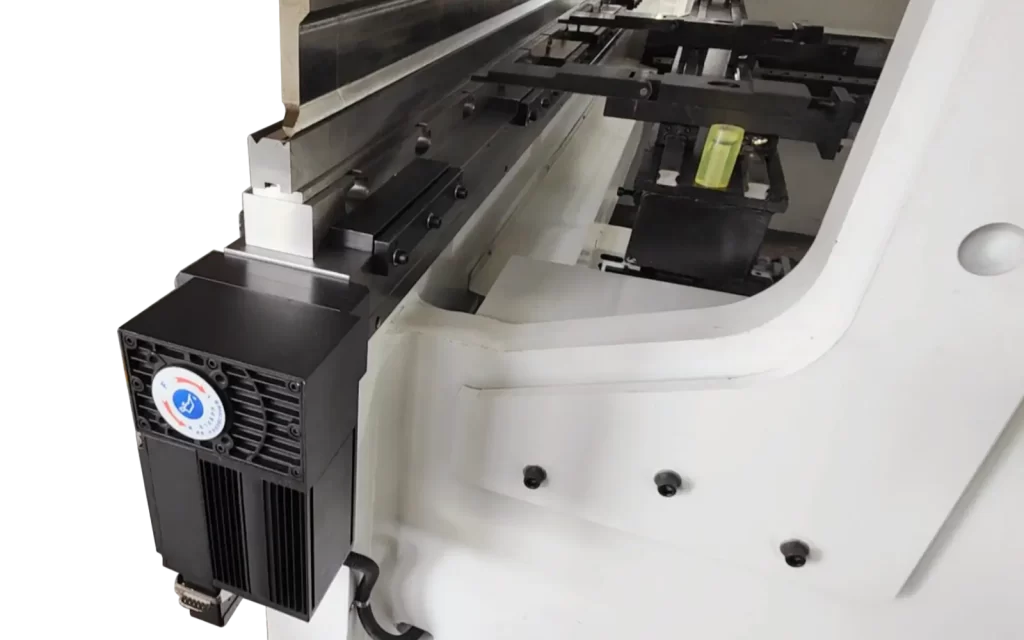
Characteristics of Mechanical Crowning
- Operator Skill Requirement: In cases involving multi-step bending operations, the operation can be relatively complex, requiring real-time localized adjustments based on experience. It demands a higher level of skill from the operator. Workers with better experience and skills may prefer this method.
- Precision: Mechanical crowning offers higher precision in the processing of long and large workpieces because the wedges can cover the entire length of the worktable, eliminating compensation blind spots. However, its precision on workpieces involving multi-step bending may not be as high as hydraulic crowning, unless manual adjustments are made.
- Maintenance: With prolonged use, wear and tear issues can arise with the wedges and screws, which are considered consumable parts. Regular replacement or maintenance is necessary, incurring additional costs. Overall, it tends to have a lower failure rate.
- Applicability: Mechanical crowning is suitable for all bending scenarios, including large-scale press brakes and large workpieces. It excels in precision for long and large workpieces and is more suitable for single-step bending workpieces.
- Price: Generally, mechanical crowning tends to have lower costs. Additionally, when setting up the dies, special customization is required based on the structure of mechanical crowning, which can add some extra costs.
Hydraulic Crowning vs. Mechanical Crowning: How to Choose?
How to choose? Let me summarize it as follows:
- Ease of Operation Comparison: Hydraulic Crowning – Wins. In multi-step bending, manual adjustments are required, and mechanical crowning demands higher experience and skill from workers, indirectly increasing labor costs. In contrast, hydraulic crowning achieves excellent results without the need for manual intervention, making it user-friendly and straightforward to operate.
- Precision Comparison: Depends on Requirements. For single-step bending of long and large workpieces, mechanical crowning excels in precision due to its minimal compensation blind spots. However, in cases requiring multi-step bending, hydraulic compensation gains the upper hand thanks to the high-frequency response and real-time compensation features of CNC hydraulic systems, and it also performs better in compensating for the elastic metal springback.
- Maintenance Comparison: Mechanical Crowning – Wins. Hydraulic crowning requires regular maintenance of the hydraulic system to prevent oil leakage. Mechanical crowning involves relatively simple maintenance, focusing on the replacement and upkeep of worn wedges and screws.
- Applicability Comparison: Depends on Requirements. Both are suitable for most batch production scenarios, but mechanical crowning performs better on large workpieces. In multi-step bending situations or significant metal springback, hydraulic crowning is more advantageous.
- Price Comparison: Minimal difference.
Which one is better? My conclusion is that there is no absolute answer, only what’s most suitable. It’s akin to the difference between manual and automatic transmission in cars, each with its own characteristics. Mechanical crowning is akin to manual transmission, while hydraulic crowning is akin to automatic transmission. Well, perhaps this is a good analogy.
Conclusion
As evident from the discussion, both hydraulic and mechanical crowning systems have their advantages and disadvantages. Enterprises should make their choices based on their specific circumstances and requirements. After years of development, both methods have matured, and today, crowning systems are a common feature in most press brakes, ranging from small to large machines. After all, the cost of upgrading this configuration is relatively low compared to the significant improvement in yield, making it a worthwhile investment.
We are a leading press brake manufacturer in China, serving the metal fabrication industry for over thirty years, with machines sold in more than forty countries worldwide. Our CNC press brake under the Velxun brand offers the option of mechanical crowning or hydraulic crowning, allowing us to recommend the best solution for your business needs. Our machines are renowned for their cost-effectiveness and high precision. Please feel free to reach out to our team of experts for inquiries.
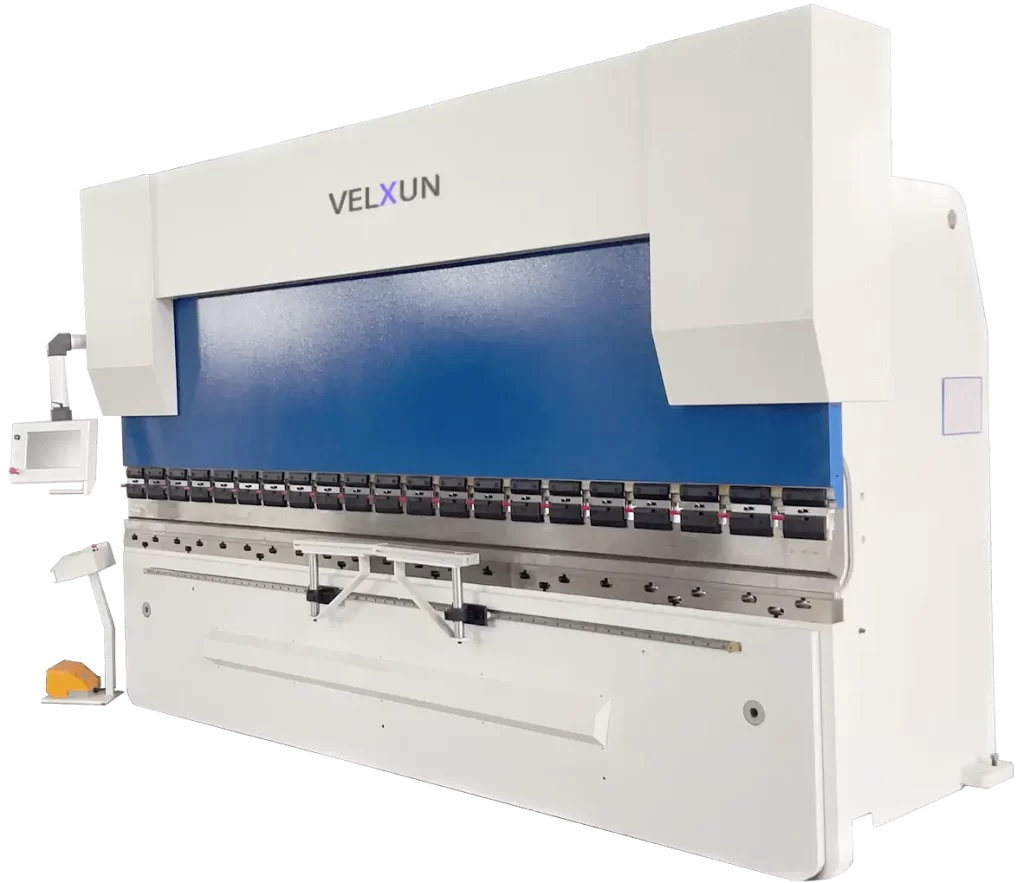
CNC Press Brake
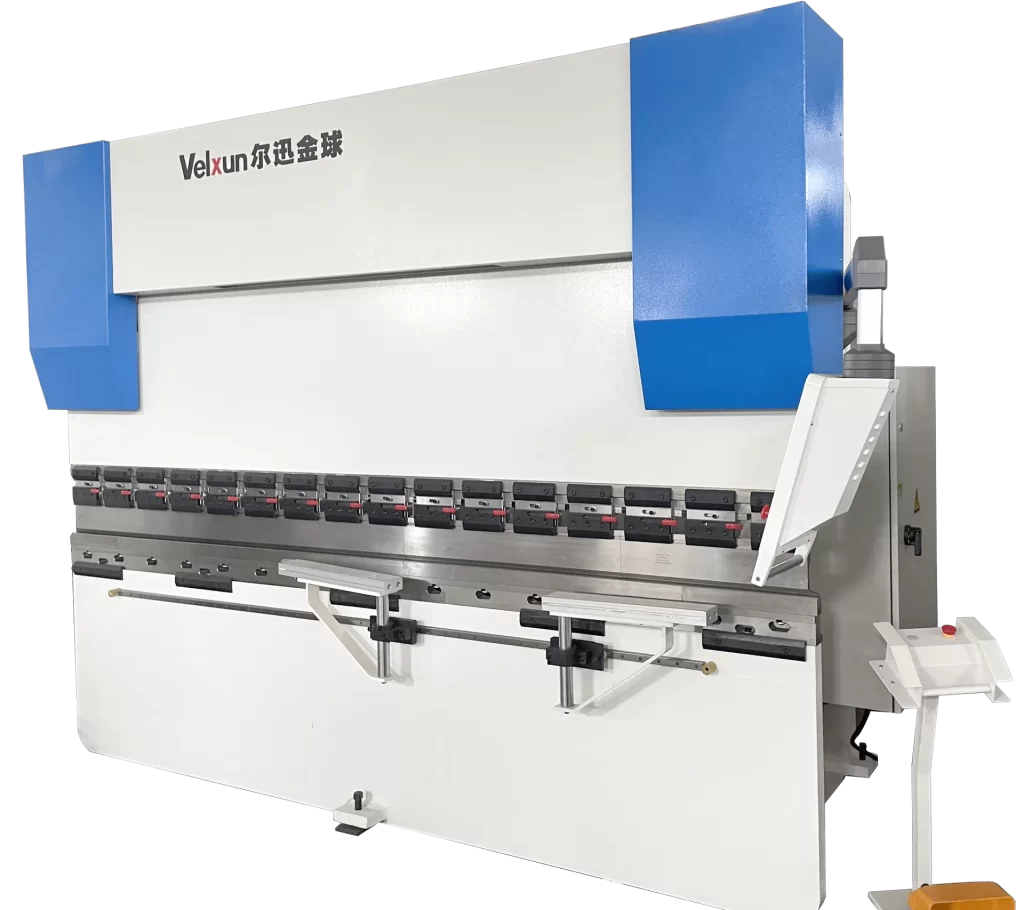