Choosing between NC and CNC press brakes often confuses many customers in the manufacturing industry. Although both machines are used for the same purpose, they have different features, capabilities, and limitations. This article aims to shed light on the differences between these two types of press brakes from various perspectives, providing assistance to both newcomers and experienced professionals in making the right choice.
What is an NC press brake?
Typically, we refer to the torsion bar synchronous press brake as an NC press brake. The torsion bar synchronous press brake utilizes a torsion bar structure for synchronous bending operations. This type consists of two torsion bars connected to the machine frame, transmitting motion through linkages and rocker arms to achieve synchronized movement of the upper and lower dies, thereby accomplishing the bending of the workpiece. Therefore, It is a mechanical forced synchronization method. Typically, it comprises a main motor and multiple clutches to transmit power and drive the tooling modules.
What is a CNC press brake?
Typically, we refer to the electro-hydraulic press brake as a CNC press brake. Electro-hydraulic press brakes employ a combination of hydraulic and electric servo systems to achieve synchronized movement of the upper and lower modules. This system comprises hydraulic cylinders, servo valves, sensors, and a control system, which uses electronic signals to achieve precise control over the position of the modules. It achieves synchronization through the use of two side servo valves. The servo motor converts rotational motion into hydraulic power, while sensors continuously monitor the positions of the dies. By utilizing sensors and feedback mechanisms, it can monitor and adjust position deviations in real time, ensuring more accurate bending angles.
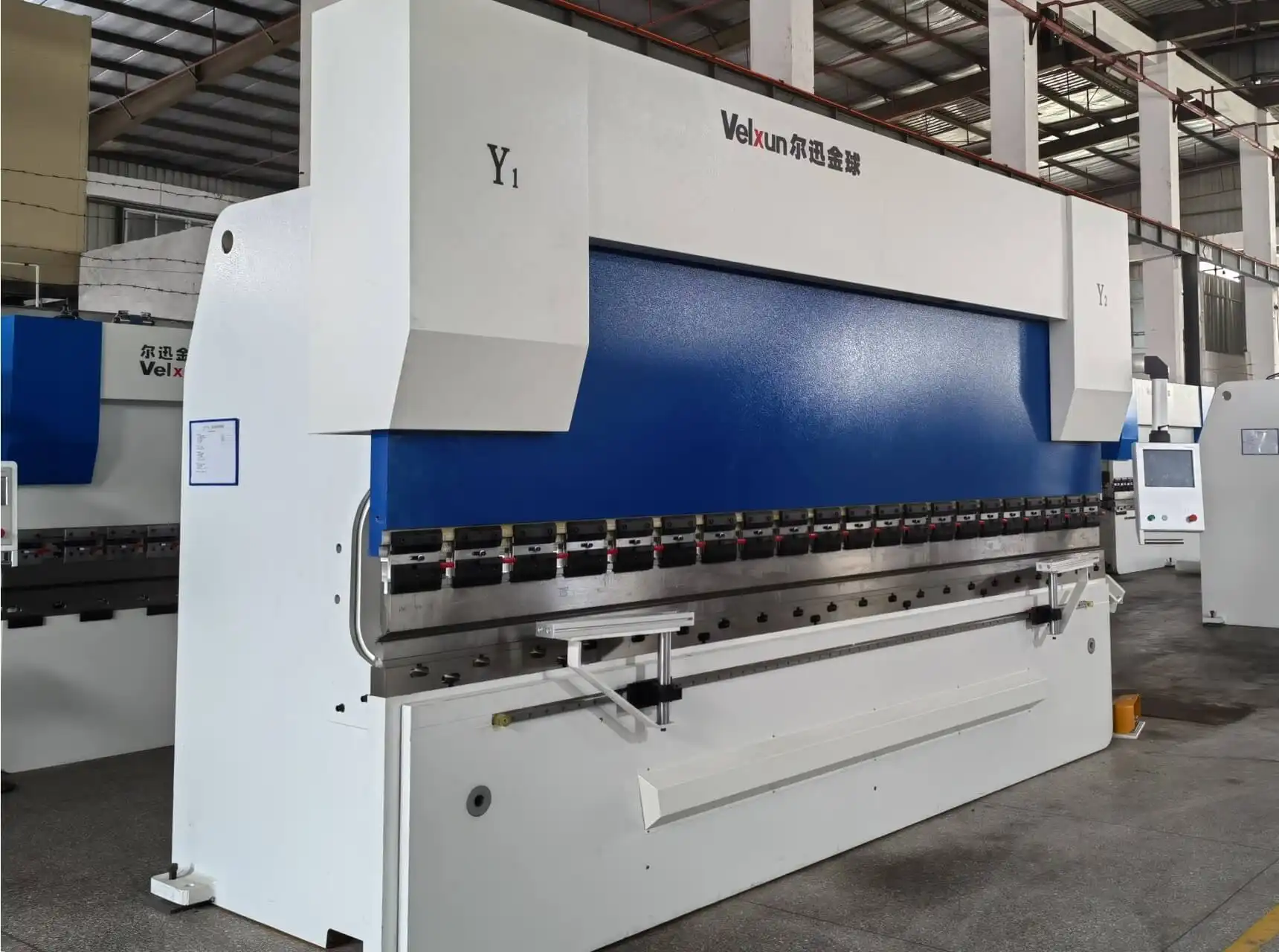
NC VS CNC Press Brake
Accuracy and Repeatability
The synchronous control of NC press brakes (torsion bar synchronous) heavily relies on mechanical transmission systems, with accuracy influenced by components such as torsion bars and linkages. Elastic deformation of the torsion bar and adjustments of the adjusting rods can lead to unsynchronized movement of the ram, affecting the precision of bending angles and flatness, typically within the range of 0.1 millimeters. They are suitable for general bending operations, particularly for smaller workpieces and applications with medium to low precision requirements. However, our NC press brake is capable of achieving ±0.01 precision, surpassing industry standards. It offers a cost-effective and high-performance solution.
CNC press brakes (electro-hydraulic) utilize a closed-loop control system, enabling high-precision synchronous bending operations. The system utilizes electro-hydraulic valves to regulate the motion of hydraulic cylinders, ensuring precise and synchronized movement of the tooling. In contrast, CNC press brakes offer higher bending precision, often achieving tolerances as small as 0.01 millimeters or even smaller and maintain better stability even after prolonged use. As a result, They are well-suited for applications that demand high precision, especially in the production of complex workpieces.
Speed and Efficiency
The torsion NC press brake’s (torsion bar synchronous) speed and responsiveness are comparatively slower due to the limitations of the mechanical torsion bar system. It typically has a fast descending speed but relatively slower ascending and return speeds, as the torsion bar system requires some time to ensure synchronization between the upper and lower modules. Altering bending speeds or performing complex multi-stage bending may require more time and adjustments. It is typically fixed at a relatively constant rate.
With advanced electric servo systems and hydraulic control technology, the CNC press brake (electro-hydraulic) offers higher bending speed and production efficiency and efficiency as they can adjust the hydraulic cylinder’s movement speed and force rapidly through the electro-hydraulic servo system. With precise electro-hydraulic control, it achieves higher bending speeds and faster work cycles, ultimately enhancing production efficiency.
Maintenance
The NC press brake (torsion bar synchronous) adopts a simple mechanical synchronization system, resulting in lower maintenance costs. Its straightforward structure eliminates the need for complex control systems. Typically, regular inspections and lubrication of critical components, such as the torsion bar, are sufficient. The cost of replacing its components is also relatively low.
Involving complex electrical and hydraulic systems, the CNC press brake (electro-hydraulic) incurs higher maintenance costs. Maintenance for it is more complex. Besides regular lubrication and inspections of key components, the control system needs to be maintained and calibrated to ensure proper operation. It necessitates regular inspections of electrical components and hydraulic elements. The cost of replacing its components is also relatively high.
Number of axes
NC press brake (torsion bar synchronous) typically has 3 main axes, which are:
a. Y-axis: It controls the up and down movement of the bending beam (top die) to achieve the bending of the workpiece. The Y-axis controls the vertical movement and is responsible for the up and down motion of the lower die during the bending operation.
b. X-axis: It controls the horizontal positioning of the back gauge to achieve workpiece alignment. The X-axis controls the backgauge movement, allowing for the positioning of the workpiece during the bending process.
c. R-axis(Optional): It controls the depth adjustment of the back gauge to achieve depth bending of the workpiece. The R-axis is the rotation axis of the backgauge, enabling the up and down movement of the backgauge to accommodate different bending requirements.
CNC press brake (electro-hydraulic) typically has more axes to provide higher flexibility and precision. A typical CNC press brake may have 4 or more main axes, including:
a. Y1-axis and Y2-axis: These are two independent control axes for dual-action cylinders, used to achieve the up and down movement of the bending beam (top die), ensuring parallel motion of the upper die and uniform bending force distribution.
b. X-axis: The X-axis controls the backgauge movement and positioning.
c. R-axis: The R-axis controls the depth adjustment of the back gauge.
d. Z1-axis and Z2-axis(Optional): These axes control the forward and backward movement of the upper die to adapt to different bending requirements.
Crowning System
Due to the differences in working principles and price positioning, NC press brakes (torsion bar synchronous) usually do not feature a crowning system. On the other hand, CNC press brakes (electro-hydraulic), with their advanced control systems and programmability, are positioned at a higher price range and can be equipped with a crowning system to achieve more precise bending compensation. The presence of a crowning system enhances the quality and accuracy of workpieces, meeting the demands of complex components. The additional cost associated with the crowning system is justified by the improved capabilities and flexibility it provides.
Price Comparison
Due to the more complex and advanced structure and control system, the CNC press brake (electro-hydraulic) generally has a higher price compared to the NC press brake. On the other hand, the NC press brake (torsion bar synchronous) has a simpler system structure and working principle, typically employing basic mechanical or electrical control systems, resulting in lower costs. The CNC press brake requires high-precision components and advanced control systems, which increase manufacturing costs and necessitate more engineering design and production expenses. In the short term, the NC series is more budget-friendly, but in the long run, the CNC series offers higher investment value.
Application Range
CNC press brakes (electro-hydraulic) are suitable for applications requiring high precision and efficiency in bending processes. They are well-suited for batch production and complex workpieces. Although they are more expensive, they provide higher processing quality and flexibility. NC press brakes (torsion bar synchronous) are suitable for general bending processes and are better suited for medium to small-scale production and simple workpieces.
Expandability
NC press brakes (torsion bar synchronous) have limited expandability and are generally not easily integrated with other equipment for tandem operations or robotic integration. On the other hand, CNC press brakes (electro-hydraulic) offer higher expandability, allowing tandem operations with other equipment and easier integration with robotics and other automation devices. After integrating automation equipment, production efficiency will significantly increase, labor costs will be reduced, and production safety issues will be avoided.
Operator Skill Requirements
Due to the CNC system and operating principles, NC press brakes (torsion bar synchronous) rely more on the experience of the workers, which may require businesses to pay higher salaries to hire more experienced workers. On the other hand, CNC press brakes (electro-hydraulic) have relatively simpler operation, requiring less experience from the operators, and they also offer higher automation levels.
Conclusion
In conclusion, businesses should choose the machine based on their specific requirements. In most scenarios, CNC press brake is superior to NC series. If the budget allows, the CNC press brake is a better choice in the long run. However, in cases of limited budget, the NC series can also meet certain processing needs. If you have any further questions, please feel free to consult us. We are more than happy to assist you.